Coaching Technology: Mobile App Improves Food Safety Culture
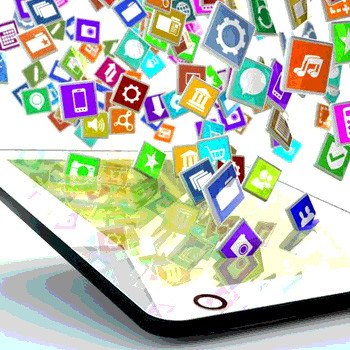
The concept of employee training in the food manufacturing and processing industry tends to follow a traditional path. Workers receive classroom instruction either through interactive technology or tools like PowerPoint and take examinations to verify comprehension. If comprehension has been achieved based on employee quiz scores, then it is onto the plant floor to presumably apply lessons learned on the job. Yet food safety deficiencies still happen, which confounds quality managers everywhere.
Analysis of shortcomings tends to reveal a sadly predictable result: for a portion of the workforce, learning does not translate into sustained, appropriate behaviors. These sporadic, inconsistent and sometimes risky deviations from the food safety plan can result in food safety issues for the company and their consumers. Why do these mistakes continue when presumably comprehension was established through training?
The answer is that total food safety compliance requires effective coaching that goes beyond training and examinations. Data indicates that employee comprehension of food safety competencies must be demonstrated and verified through skilled coaching observations of behavior to reduce risks of operational nonconformance. What has changed is the application of tablet technology to coaching employee behaviors. Thanks to the technology, coaching that was previously a time-consuming task can be effective without reams of documents and notes awaiting data entry. Imagine being able to install job specific process checks through mobile apps, conduct those checks using a tablet and wirelessly sync the results for reporting, corrective action reviews and validation.
Actually, there is no need to imagine such technology because it is already here. There’s an app for that.
The Evolution of Food Safety Training
For too long, food safety training limited to the classroom has been cumbersome and not always effective. Usually, concepts were delivered through PowerPoint presentations in a typical lecture format. Paperwork such as spreadsheets represented the documentation for employee attendance and examination results. All too often, key paperwork selected by the auditor was not readily accessible—a common training program audit deficiency.
All of that changed with the development of intuitive electronic teaching systems that provided instantaneous record-keeping through learning management systems. Companies that adopted this interactive technology found that employees became more active learning participants rather than listeners of lectures that they may not have comprehended.
Not all companies, however, have adopted the advanced technology. As a result, concepts presumably learned through training and examinations are not always applied on the job leading to potential food safety issues. Clearly, there is a “disconnect” between the learning achieved in the classroom and non-conformances exhibited during production.
Focus on Behavioral Change
The number of food safety incidents explains why key employee behavior should be periodically monitored during operations regardless of how well workers performed on their training quizzes. Behavior observance and measurement are part and parcel of a coaching strategy to help ensure safety and lessen compliance risks. But can coaching sustainably change the behavior of front-line workers in the food industry workplace?
Findings from an independent study in 2013 indicate that it can. The study conducted at four U.S. food processing plants deconstructed various processes into steps and set employee actions for each step. A baseline level was established for each step so that each employee’s action could be observed, measured and documented. Supervisors were required to make corrective observations (coaching) until the change of behavior could be validated. The results: Compliance increased by substantial margins when coaching was added to training. At a Wisconsin meat processing facility, baseline compliance of 74 percent after training increased to 93 percent following extended corrective observations. Thanks to coaching conducted by informed supervisors, employees developed a culture of doing the right thing and were able to coach new employees who joined their production line.
The importance of coaching in the training process has been corroborated with the release of the 2014 Global Food Safety Training Survey. The informative survey included questions about coaching for the first time, understandable given that a number of respondents reported audits showing major deficiencies in employee comprehension. Nearly 40 percent of the respondents reported using coaching as a training tool largely due to observance of poor behavioral habits despite what was supposedly covered in classroom training.
Yet to successfully change behavior, coaching has to be more than a supervisor with pen and clipboard issuing and writing corrective comments. Today’s technology has provided a ground-breaking answer in the form of that most easily-accessible program—the mobile app.
Mobile App Coaching Technology
One innovative and ground-breaking app for food safety coaching is available for tablet technologies such as the iPad. Corrective observations made by supervisors are instantaneously entered into the company’s employee record database, eliminating cumbersome use of paper and extra data entry. Like many of today’s mobile apps, the wireless system is intuitive with algorithms that can document and report root cause analysis, vital for influencing and changing sustained behavior. After all, the best use of the technology may well be identification of the problem’s root cause before applying appropriate corrective actions to fully address deficiencies.
The mobile app operates with templates that provide a variety of formatted questions on processes integral to food safety compliance such as hand-washing, sanitation, etc. Different scoring methods are offered for accurate verification that behavior is positively influenced.
This technological advancement, the first to be tied directly to training, simplifies and documents electronically while streamlining workflows and audits—a blessing for those who previously had to deal with reams of paperwork. The app has drawn praise for ensuring that best practices in food safety and production are always followed while improving worker productivity.
“It helps our accountability and enhances our training program,” said Melody Magallanez, learning leader of Green Mountain Coffee Roasters. “It has saved us money with our internal training from site to site.”
“To be able to take this to the floor and evaluate my associates as they’re doing their jobs is not only a benefit to us but a benefit for everybody,” said Albert Nye, quality assurance and sanitation supervisor, Cott Beverages.
It is not a stretch to suggest that the emergence of mobile app technology may revolutionize the entire concept of training. Classroom learning, no matter how effective, does not always translate to the desired behavior in the food processing workplace. As such, companies are rightly concerned about employee adherence to their comprehensive food safety program, quality assurance, workplace compliance and records documentation. Coaching mobile app technology is designed to resolve those concerns through customization to meet individual plant needs.
Electronic functionality makes the technology a vital tool for identifying operational challenges that may not be apparent, resolving them through coaching and recording them into a system that satisfies audits and compliance requirements. Such advancements provide a unique tool to measure training effectiveness reducing the demand on quality control’s limited time and resources. The technology measures and documents behavior change for the betterment of the company and the safety of its consumers and is a great tool for reinforcing positive behaviors.
Laura Dunn Nelson is vice president, technical services, for Alchemy Systems, Austin, TX. Alchemy is a global leader of innovative technologies and services designed to align employee behavior with a company’s quality and safety commitments. For more information, please visit www.alchemysystems.com.
Looking for a reprint of this article?
From high-res PDFs to custom plaques, order your copy today!