The 40th Anniversary of the Bar Code: An Update from GS1 US
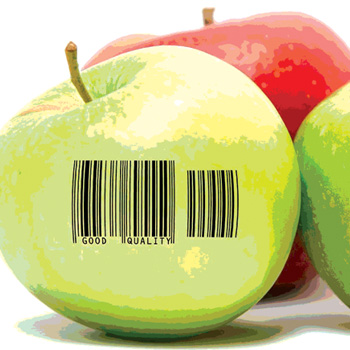
Forty years ago, a pack of Wrigley’s chewing gum labeled with a Universal Product Code bar code was scanned at an Ohio supermarket. For the first time in history, the grocery industry was able to electronically capture information about an item at the point of sale.
Today, it’s hard to imagine life without bar codes.
In the food industry, bar codes are not only used to identify and capture product information, they also lay the groundwork for companies to establish their traceability programs and enhance food safety operations. The need for improved traceability has grown only more urgent as a result of the 2011 Food Safety Modernization Act, which has empowered the U.S. Food and Drug Administration (FDA) to establish a food product tracing system and mandate recalls as necessary.
GS1 US is a standards organization dedicated to improving supply chain visibility for all stakeholders along the product’s journey from source to point of consumption. The organization plays an ongoing, central role in driving industry discussions aimed at leveraging existing investments in the use of GS1 Standards to enhance traceability processes across all food categories.
Today, more than 2 million companies doing business in 150 countries across more than 25 industries use GS1 Standards for unique product identification, information capture and data sharing among trading partners, and about 5 billion bar codes are scanned every day at the point of sale. Growing consumer demand for accurate and complete information about what’s in our food and where it came from is another important factor in the increased focus on traceability and food safety.
Two industrywide initiatives—in which GS1 US plays a strong role—have focused exclusively on these efforts: the Produce Traceability Initiative and the Foodservice GS1 US Standards
Initiative.
The Produce Traceability Initiative
The Produce Traceability Initiative (PTI), spearheaded by the Canadian Produce Marketing Association, GS1 US, Produce Marketing Association and United Fresh Produce Association, is leading the broader fresh food industry in establishing milestone-based road maps for case-level electronic traceability. With senior leadership representing buyers as well as growers, packers and shippers, PTI was launched in 2008 on the heels of several deadly foodborne illness outbreaks as a response to the industry’s growing need to streamline traceability and food safety processes for produce.
The cost of recalls also influenced the produce industry to take action. A 2006 spinach recall cost the spinach industry over $400 million in damages, according to documentation from the Produce Safety Project, a collaboration between the Pew Charitable Trusts and Georgetown University and as cited in a GS1 US white paper entitled Integrated Traceability in Fresh Foods: Ripe Opportunities for Real Results. In 2007, a mistaken Salmonella finding in tomatoes cost that industry $500 million, the paper reported.
Earlier this year, FDA released the Institute of Food Technologists (IFT)’s traceability recommendations and asked for industry comments in preparation for the proposed traceability rules the agency is set to release in the coming months. GS1 US, along with PTI’s three other administering organizations, submitted joint comments in support of IFT’s recommendations based on the work PTI volunteer organizations have done in understanding industry needs and developing best practices for case-level electronic traceability. In addition, PTI efforts continue to facilitate market-based solutions to enhance overall tracking efficiency and speed within the produce industry.
To present more standards-based feedback to FDA, GS1 US offered additional comments clarifying how unique product identification with GS1 Standards helps companies establish a standards-based foundation on which collaborative supply chain solutions (like track and trace) are built. Effective collaboration between trading partners is based on the use of uniform data requirements and standards for both item- and case-level electronic traceability and supply chain visibility.
While produce suppliers have paved the way for PTI’s success, it has been critical to gain buyers’ support to drive traceability implementations in both the grocery and foodservice channels. Walmart has led efforts to adopt uniform standards in several product categories. In fact, the grocery giant’s recent announcement (jointly issued with Sam’s Club) requiring their suppliers to use PTI case labels has spurred additional interest and activity in traceability standards for the industry. As part of Walmart’s strengthened focus on the quality and safety of the produce it sells, the company has asked that its suppliers follow PTI guidelines by November 1. The increasing percentage of produce cases marked with PTI labels, coupled with other large retailers beginning to ask their suppliers to become PTI compliant, illustrates the momentum the fresh foods industry is seeing in improving product traceability.
In addition to PTI’s work on traceability in produce, other fresh food subsectors, including meat and poultry, seafood, and dairy, deli and bakery, have also progressed steadily in this arena, developing implementation guidelines and best practices.
More globally, GS1 US has become one of several founding partners of IFT’s new Global Food Traceability Center, slated to serve as the authoritative, scientific and unbiased resource for food traceability.
GS1 US is not only in full alignment with the mission and goals of the Global Food Traceability Center, it also shares the belief that only through education, information sharing and a collaborative approach can the food industry strengthen its capabilities for effective and efficient traceability processes worldwide.
The Foodservice GS1 US Standards Initiative
In 2009, GS1 US and 55 leading manufacturers, distributors and operators, along with the National Restaurant Association, the International Foodservice Distributors Association and the International Food Manufacturers Association, launched the Foodservice GS1 US Standards Initiative to improve supply chain efficiencies, food safety and traceability and product information (including nutritionals and allergens) in the foodservice industry. The goal of the initiative is to have 75 percent of the foodservice industry (measured by revenue) voluntarily adopt GS1 Standards by 2015. The Foodservice GS1 US Standards Initiative has now more than surpassed its halfway mark.
Since its launch in 2009, some of the largest manufacturers, distributors and operators in the industry have adopted GS1 Standards. Manufacturers have put bar codes on their products using Global Trade Item Numbers (GTINs) to identify products, while Global Location Numbers (GLNs) identify specific locations throughout the supply chain. The Global Data Synchronization Network (GDSN) is a central database “in the cloud” of more than 300,000 foodservice products on the market where manufacturers publish the most up-to-date product information. Distributors and operators can access the network—through GS1-certified data pools—to receive this important information.
The initiative has far-reaching benefits for all supply chain partners. Manufacturers can take all the information they have for one product and load it into one place—the GDSN—which sends that information to all of its customers at once. Distributors now have one, easily accessible source of information for products, and they can scan bar codes on products to improve their receiving and shipping processes as well as their ability to trace product through the supply chain. Operators also have “one source of truth” for product information and traceability.
The GS1-128 bar code, which includes GTINs for product identification as well as batch and lot numbers, production dates and other product attributes, lays the groundwork for distributors and operators alike to know where their food came from, which is helpful for recalls and inventory management. With more recalls and contaminated food situations, it is imperative that supply chain partners identify the source of the contaminated food and remove potentially harmful products from the supply chain as quickly as possible. This level of supply chain visibility helps isolate and remove impacted product from store shelves.
While manufacturers have been particularly active in GS1 Standards adoption, as evident by recent warehouse assessments showing nearly 75 percent of products carrying GS1 bar codes, in the last year, large restaurant chains and other foodservice operators have been leading the forward momentum. DineEquity, the parent company for IHOP and Applebee’s, has requested that their proprietary suppliers begin using GS1-128 bar codes so they can trace their products through the supply chain. Darden Restaurants, the Unified Foodservice Purchasing Co-Op (Yum! Brands), Quality Supply Chain Co-Op Inc. (Wendy’s) and the Independent Purchasing Cooperative (Subway) have also been leading the adoption effort.
The industry has also seen phenomenal growth in the number of GDSN subscribers. Since its start in 2009, the number of subscribers has grown from a mere 191 to nearly 3,000 this summer. In just the past year, the number of foodservice products with published information in the system has more than doubled, now at 322,000 products. In the near future, this number is expected to reach more than 1 million.
Distributors in particular are beginning to use the GDSN extensively to access the most accurate product information for their catalogs and customers.
There is a huge demand now for more accurate data—studies have shown that food product data in the past was not as accurate as it could or should have been. This push toward improving product information will only continue in 2014. Without a central database like the GDSN, those looking for product information are forced to scour manufacturer websites to try to source these data, and there’s no guarantee they’re always updated. Knowing a product’s weight and dimensions is one thing, but the ability to see standardized, professional images of products and know the nutritionals and allergens of the product are even better. As consumers grow more concerned about allergens like gluten (see p. 30), access to better product information is even more vital.
Compass Group has been a leader in this area, actively using the GDSN for nutritional, allergen and other product information to develop menus for patients in the healthcare segment, and to adhere to tightening regulations in the K–12 school foodservice sector.
Beginning this year and carrying into next, the industry has turned its focus toward GLNs to identify locations in the supply chain. A manufacturer may have multiple plants, so it’s important to identify which plant manufactured the product, especially in the case of a recall. Distributors will also use GLNs to identify where they shipped their products, drilling down to the specific store for a large restaurant chain that might have thousands of units nationwide. Right now, locations are identified by name only in many instances. Giving every location a computer-friendly number again helps supply chain partners use the same language. Together, the GS1-128 bar code and GLN will provide a more complete traceability picture.
Early adopters and those involved in the fresh food and foodservice initiatives strongly believe GS1 Standards are the only way to firmly establish “one source of truth” for all food products and locations in the supply chain. GS1 Standards help the entire industry speak the same language to reduce confusion, errors and costs as well as improve the safety of our food supply.
Dennis Harrison is senior vice president, foodservice industry engagement, at GS1 US.
Angela Fernandez is vice president, retail/consumer packaged goods, at GS1 US.
GS1 US is the not-for-profit organization that helps U.S.-based industries and businesses adopt and use GS1 supply chain standards, making the food supply chain more visible, secure and sustainable. Learn more at www.gs1us.org or contact GS1 US at info@gs1us.org.
Looking for a reprint of this article?
From high-res PDFs to custom plaques, order your copy today!