New Survey of Processing Companies Reveals Uncertainty of FSMA Implications
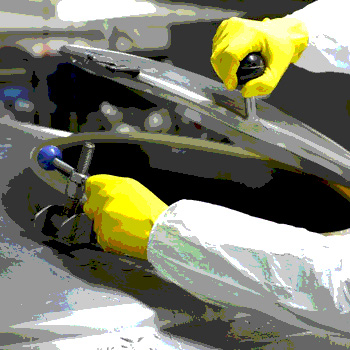
As most business owners working within heavily regulated industries can contend, keeping up with the latest rules, regulations and guidelines can be difficult. A testament to this widely held belief? The Food Safety Modernization Act (FSMA).
Although FSMA was signed into law by President Barack Obama on January 4, 2011, the laws that made up the bill were not enforced until this January.
This incremental introduction of the new law was meant to allow organizations time to prepare for new regulatory practices. Unfortunately, the measured phasing has caused confusion and slight panic—a common theme found in a study that was conducted this year.
Survey results found that most of the process manufacturers surveyed are still unsure how the new law and its accompanying regulatory changes will affect their business and production processes.
This looming uncertainty was confirmed when 44 percent of surveyed respondents listed their biggest concern regarding new FSMA regulations as “uncertain or unclear implementations.” The data confirms that food and beverage manufacturers are mostly aware of the new bill, but are relatively uncertain about how the new requirements will encourage regulatory change.
In fact, 71 percent of those surveyed stated that they were aware that FSMA will affect their production processes; however, when asked how, the most common response was “unsure” (47 percent of respondents).
In addition to being unsure about guideline changes, many manufacturers are actually unconcerned and/or unprepared to handle the regulatory changes. FDA has stated that most plants will need to make certain strides to accommodate the new bill’s policies. This includes increasing capital expenditures in order to upgrade current technology.
However, 45 percent of surveyed respondents stated that they have not currently taken into consideration the planning or budgeting that must address the FSMA guidelines. Moreover, a shocking 76 percent of all respondents stated that they do not plan on making changes to meet the guidelines—which could include increasing number of staff and updating resources.
One of FSMA’s conditions that should draw a great deal of attention is the stipulation that mock recalls be conducted more frequently than they had in years past. A recall of this nature requires time—days or even weeks—and the heavy involvement of increased staff from multiple departments. Knowing this, increased staff, resources, and technology seem necessary to accommodate impending mock recalls and properly abide by FSMA.
It is important that plants are prepared for this aspect of FSMA because the law also allows FDA to levy fines and access fees, where appropriate. Although many plant owners do not believe that this change warrants any threat, the recent shutdown of a New Mexico plant should encourage other food and drink manufacturers to pay heed.
FDA closed the New Mexico Sunland Inc. plant last November due to incomplete regulatory revisions. Had the business invested in new and adaptable manufacturing technologies, this may not have been a problem. Businesses that begin to budget for new resources will be more prepared for the new FDA regulations and more prepared to handle any additional guidelines that FDA might enforce.
The hesitation that many companies have in regards to updating technologies or increasing resources may be a direct result of uneven economic recovery. Companies have generally held more cash as economic indicators such as unemployment have fluctuated wildly. Any investments being made today are directly related to cost cutting or revenue improving.
One of the main factors that might be preventing companies from updating their plants is the current technology—or lack thereof—that most currently use to track and manage their production processes. Many companies still rely on basic programs and simple spreadsheets to maintain production information. This trend is supported in survey responses. While 76 percent of respondents did say they currently use a quality control management system, nearly 45 percent of respondents reported using spreadsheets or other manual processes to manage traceability, quality and inventory issues.
Unfortunately, FSMA regulations explicitly define the need for improved technology for record keeping in order to keep up with the newly introduced auditing system. Skepticism that FSMA will be actively enforced is another reason that most companies may not planning on improving their business practices based solely on new requirements. While this might have been the case in laws past, plant owners and employees alike should be aware that the Congressional Budget Office has announced a budget of approximately $280 million per year in order to maintain and enforce the new FSMA regulations.
Without knowing the budget associated with enforcing FSMA, a whopping 76 percent of all surveyed respondents stated that they would not start using any kind of automated system. The reason for the resistance? Most responded that their systems are already compliant with the new regulations.
This disconnect, evident throughout the survey, is indicative of the need for the FDA to better educate plant owners on the regulations associated with specific laws, as well as the need to better enforce the laws as they are enacted. This is especially true of the FSMA, since facilities managers will be burdened with improving current technology so that they pass any audit—mock or otherwise—and to ensure that their products are not hampered with quality issues throughout the production process.
The final and most compelling reason to update technology is that once rules and regulatory laws are well defined—as they are in FSMA—litigation against manufacturers becomes more common. When there are explicit laws that seem to be broken, lawyers can easily win a case through careful nitpicking and execution.
Better safe than sorry holds especially true in this striking situation.
Sudhakar Kaup has over 18 years of experience in designing and implementing solutions for the manufacturing industry.
Looking for a reprint of this article?
From high-res PDFs to custom plaques, order your copy today!