Point-Counterpoint: The Produce Traceability Initiative
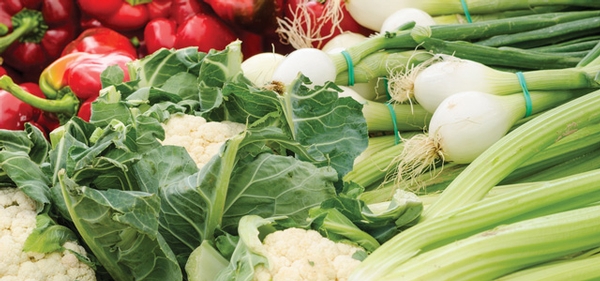
The Canadian Produce Marketing Association, Produce Marketing Association (PMA) and United Fresh Produce Association formed the Produce Traceability Initiative (PTI) in 2007 to help produce companies and their buyer partners move toward achieving whole-chain traceability.[1] Initially guided by a committee of more than 50 produce retailers, wholesalers, distributors, packer-shippers and growers, an action plan was developed to achieve whole-chain, electronic traceability by 2012. GS1 US joined PTI’s administering organizations in 2010. That same year, a leadership council was formed to direct PTI’s activities moving forward, including the development of best practices, pilot studies to address barriers to both implementation and transparent communication with supply chain members.
PTI is designed to help the produce industry maximize the effectiveness of current traceability procedures, while developing a standardized approach to enhance these systems for the future.
While most produce companies have embraced PTI and have begun to implement its suggested best practices, some are still resistant. We offer this point-counterpoint to address the lingering disparate perspectives on PTI and offer a glimpse into common ground between these differing viewpoints.
Taking the Point position is Gary Wishnatzki of Wish Farms; taking the Counterpoint side is Steve Warshawer, National Good Food Network food safety coordinator and consultant to the Wallace Center.
Gary Wishnatzki: It has been a long journey to get the entire produce supply chain on board with PTI. I believe that to have an efficient and effective traceability system, everyone needs to be speaking the same language.
Fortunately, the aviation industry figured that out fairly early on. English is the de facto international language of civil aviation. Every pilot and air traffic controller speak it. Can you imagine the chaos there would be in the sky if there wasn’t this standardization?
PTI has been evolving for nearly 10 years, and there has been a very inclusive approach taken by the PMA leadership to shape the standards and best practices. PTI may not be the perfect system for everyone and it may not be the best solution for every application, but it is a standard that has been hammered out through tens of thousands of hours of produce industry volunteers’ time.
It was the consensus of everyone involved that we needed a common language that can be easily communicated throughout the entire supply chain. In online meetings about PTI, it was a widely held belief that the produce industry should formulate traceability standards that the U.S. Food and Drug Administration [FDA], in their implementation of the Food Safety Modernization Act [FSMA], could “coat-tail” on. In conversations with FDA officials, it became clear that they were looking to the industry to craft traceability standards and they were not interested in constructing the rules. It seemed far less likely that the FDA would impose any guidelines that we wouldn’t agree with if we created a traceability system they could simply inherit. I don’t expect that we will see anything coming out of the Produce Rules that will be inconsistent with PTI, for that reason.
PTI is not complicated to implement. The primary challenge for growers is that there is an added cost. My company, Wish Farms, is a marketer, but I also own farming operations. I am very sensitive to burdening growers with additional costs.
Before PTI was formalized, we were already doing item-level traceability on strawberries. The system that we have now branded as “How’s My Picking” provides valuable information that we view as an accountability system, and traceability is a beneficial byproduct. We can tie back consumer feedback to an exact harvest event and a picker in the field. We see real value in that, and we can point to cost savings because of it. Whereas PTI we view as an insurance policy that would allow us to do a precise recall and potentially limit the fallout on a larger scale. There were some challenges in melding our item-level system with case-level labels, but we were able to design a seamless system that incorporates both. Item-level traceability is needed to pinpoint the exact source of a problem. Case-level traceability is necessary to facilitate an organized recall.
The Tester Amendment to FSMA contains flawed thinking in that small growers have less risk of having a food safety issue. There is no reason that any grower should be exempt from food safety guidelines, including traceability. A small grower selling their product into the marketplace where it will end up on a family’s table should have to play by the same rules as everyone else. There are many low-cost solutions to print labels. One thing the federal government could do is provide subsidies to small growers to help them obtain a GS1 number. The bottom line is: If you are in the farming business, you should be taking precautions to ensure your produce is safe and traceable regardless of the size of your operation.
Retailers will need to do their part to make sure that the industry continues moving toward full implementation. It does little good if growers go through the cost of complying with PTI if warehouses are not capturing the information and tracking it through their systems. PTI affords the possibility of precision recalls if retailers follow through on implementation in their organizations. Otherwise, recalls will be done by casting a much larger net and will be much more costly. This is what growers are trying to protect themselves against by using PTI. I applaud those retailers that require PTI compliance and who are also taking steps to track the produce through to their stores.
For our organization, there is no turning back on PTI. When the call comes in to Wish Farms’ control tower, we will not be speaking Greek.
Steve Warshawer: I have been asked to offer a counterpoint to the case for PTI. I am viewing PTI specifically from the perspective of operations that are new to the supply chain, often smaller and generally operating with simple and manual record-keeping systems. Some groups within this sector have religious and/or philosophical objections to mechanization/technology/automation. Many are struggling with the costs of starting businesses in ways that give them a higher likelihood of success. Many are new to the supply chain and its requirements. Most recognize that “your” (supply chain) customers want “their” food, and that “your” customers appreciate the opportunity to purchase “their” food at familiar locations where they will be shopping or eating anyway.
The case for traceability is sound. Any businessperson who has explored the pros and cons of traceability can see that it benefits his/her business. The question is, “How can a business address its traceability needs in a scale- and cost-appropriate fashion?” This is where so far PTI loses traction: It asks too much and at too great a cost for a very large number of mostly smaller and new businesses.
The top-line goal of “electronic” traceability creates the disconnect described above. There is no doubt that PTI is helping larger supply chain partners and their intermediaries and growers and packers maintain superior knowledge about the sources and movement of produce through the supply chain. This information helps dramatically in the event a food safety or quality issue has been identified. Even over the great distances that product has moved, offending product can be quickly tracked, the public can better informed and protected, and the reputation of the product or commodity in question and the businesses who have handled it can be preserved. Electronic implementation integrates well with the scale and systems of the large supply chain players.
In order for PTI to gain “universal” acceptance, if by “universal” we mean the full range of operations from large to small, then there must be further refinements to the PTI implementation process and there needs to be a cost (sharing) structure. The challenge of the electronic side of universal acceptance begins and will end with the question of at what cost and at whose cost is this system implemented?
Some of the major factors that influence the PTI operational cost include:
• Acquisition of a GS1 company prefix
• Hardware and software to build GTIN [global trade item number] or cost to join a GS1 partner’s connection
• Cost of prefarm-gate adaptation of harvest and record-keeping to produce initial case data
• Training costs and maintenance costs for current technology
Estimate and add up these costs, and if all of those that pertain to farm-level implementation are borne by the farm, then only farms of a certain size and technology-readiness will be able to meet PTI requirements and enter the supply chain. This is fine if this is what the supply chain players want. But if the notion mentioned above is correct, that “your” customers want “our” food, then something has to give.
There is no disagreement over the notion that traceability systems are invaluable and can benefit all supply chain players, regardless of scale. A consistent language for describing the contents of a case, in easy-to-read and easily accessible form, is beneficial particularly to fresh/perishable product suppliers. In my business, I have implemented a simple traceability system for our shell eggs that in one instance helped us quickly track down a quality issue, isolate where it occurred, which customers were affected, recover affected product and retrain the individuals responsible for the issue. The speed with which we were able to respond to the problem, and the clarity of explanation we were able to offer at the end of the process, supported our reputation in the small community that we serve. The success of the simple system has led to adoption of similar methods in other fresh-product distribution in our community. But no aspect of this process is electronic. Labels are handmade, and case data are transferred to invoices by hand.
GS1 barcoding is used for our eggs and by nearly all nonproduce vendors, (dairy, baked goods and more), but case-level information is not added. The GS1 barcode is unique only to the company and product. It is not unique for batch and lot coding. In adding case-specific data to the GS1-based barcode, a far more sophisticated and costly level of equipment, system and process is needed.
Currently, our local food distributor maintains GS1 membership at a level that allows it to issue company and item codes to any small local producer who needs one. This is not part of an exclusivity arrangement; it is a “community service.” One that has very little cost to the distributor. Would it make sense for any/all/every distributor to offer this service to its suppliers who need it?
So far, this service has not been extended to produce suppliers. The discussion of how to extend this service is focused on developing a system where human-readable, handwritten information could be entered into a portable scan/print unit at the receiving location and the resulting tag applied to the case of product. The coming fall and winter will allow time to further explore this idea.
To make this interface more efficient, it may make sense to assign a company code to each farm and help them acquire labels that include their name and address and a company ID barcode.
If that works, then it would also be conceivable to add to the label a product code (GTIN), but the printing costs rise as more inventory is created in anticipation of product not yet harvested. So maybe the product GTIN is a separate label, and any grower producing that item can use a common GTIN label. At that point, the manual label content could be date and lot code only, and the manual data entry at receiving point would be much reduced.
To advance its goal of universal acceptance of an electronic traceability standard, PTI leadership might want to invest in and pilot ideas like this one, where manual on-farm systems are captured in electronic form at the point in the supply chain where the hardware, software and human resources exist to efficiently effect that transition.
All of us in business, regardless of our size, want to do what is best for our customer. That commitment is at the core of every successful business. This is as true in the area of food safety as it is in any aspect of the food production and supply process. The PTI vision of traceability is one that all farmers can play a role in but cannot shoulder the costs alone. In the end, all the farmer should need to do is to provide the next step in the supply chain with what it needs to ensure full trace-forward. A legible label that includes basic details and in turn links to the farm’s internal harvest and pack records meets that description. The FSMA Produce Rule will require “one step forward, one step back.” How to best achieve the automation of the detail that the supply chain wants, and that PTI calls for, will likely require breaking the overall problem down into smaller pieces and sharing costs to alleviate burdens on the primary, original producer wherever possible.
Your customers want our food. And you want the best trace information that you can get. Working together under PTI with some creative implementation strategies, there should be a win-win for all.
Food Safety Magazine: While there is strong agreement about the virtues of traceability, questions of how this should be achieved may require additional compromises across the produce industry. At Food Safety Magazine, we believe that ongoing discussions among producers of all sizes across the supply chain provide the best chance that industry can present prospective solutions to regulators while guaranteeing a universally high standard for food safety from farm to market.
We hope that the ideas presented in this article lead to a fruitful resolution of the challenges that remain for produce supply chain members seeking to implement PTI.
Gary Wishnatzki is founder of Wish Farms, a year-round supplier of strawberries and blueberries, with sales deals throughout North and South America.
Steve Warshawer is thes National Good Food Network food safety coordinator and consultant to the Wallace Center.
Reference
1. www.producetraceability.org.
Looking for a reprint of this article?
From high-res PDFs to custom plaques, order your copy today!