Constraints to HACCP Implementation in Developing Countries, Part III
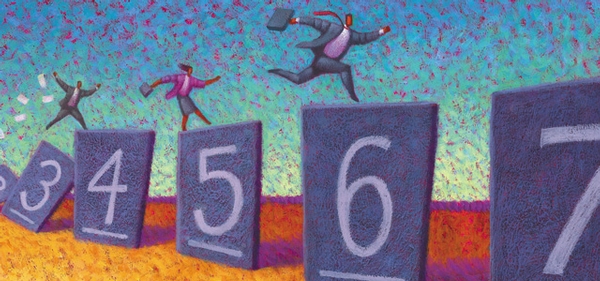
In Part I of this series, (April/May 2002, p. 36, Food Safety Magazine), the authors described why HACCP development and implementation in developing countries tend to lag behind programs in developed nations. Part II, (October/November 2002), focused on regulatory and educational issues in such countries. This final installment explores the cultural and technical food production issues faced by developing countries, and advises how developed nations may be able to help.
Cultural Issues
For any food safety program to move forward, universal support is required. What has helped drive such programs in developed nations is increased awareness of safety issues and consumer demand for safe and wholesome products. This environment has created an awareness within the food industry that "food safety is good business." However, this is certainly not the case in many developing nations. Cultural issues in these countries often are barriers to the
Hygiene and Health. Perhaps the greatest barrier to the production of safe food in developing nations is the lack of understanding of the relationship between proper hygiene and good health. For example, the average person simply does not understand why handwashing is so important. Or, to cite the example from Part I, General Foods had to go so far as to teach their employees how to use the toilet. Education must begin with a commitment from government. Regulators in developing nations can influence curricula and what is printed, broadcast or televised by the media more easily than those in some developed nations. Educators must begin emphasizing good hygiene at the grade school level. Radio, television and newspapers need to cover hygiene topics and make those lessons applicable. It may be best to target women, especially mothers. We say this based on experiences in Egypt where we learned that women working in fruit and vegetable packing houses were quite keen on learning about basic hygiene, especially when the instructors took the tack that such knowledge can help them keep their own children healthier. Again, the key to education of the public is making that experience applicable to the audience. This is where using simple tools like the Glo-Germ products or Petri plates with media can be so valuable.
Delegation. The next point pertaining to culture is directly applicable to the businesses themselves. In many developing nations, both home life and businesses are patriarchal (or matriarchal). There is one "boss" whose word is the law. People growing up in such an environment become followers and are afraid to make decisions. Creativity also is stifled, so people tend not to look for better ways to do things, but are content with the status quo. Such an attitude may work at home, but it is dangerous in a business environment. Any individual who manages a business must learn to delegate and needs to look for people who can not only do work, but will make decisions when decisions must be made. The "big boss" can set policy and determine in what direction the company should go, but if he (or she) is afraid of delegating responsibility, growth will be slow.
This mentality is especially important when implementing a system like Hazard Analysis & Critical Control Points (HACCP), since there are many people who must be entrusted to make the day-to-day decisions that make the program work. Getting the older business types to change is often difficult, but since the eldest son or daughter often is the heir apparent in such programs, efforts should focus on these persons. Again, business and technical school educators need to emphasize the importance of delegation and cooperation in being successful.
Sensitivity. Overcoming constraints within the culture of developing nations becomes a more sympathetic and effective effort for the locals when their traditions and culture are considered and respected. Although many developing nations have empowered women, the realities that exist in each country must be evaluated and considered. For example, in one country in Southeast Asia, women were taught how to cultivate their home gardens and were encouraged to sell their excess crops in the public market. Those who followed this advice and were successful found themselves ostracized from the "male dominated community" because they had become the breadwinners, a situation that was not appreciated by their spouses. It took time and a strong educational campaign to make all those participating to realize the benefits of the project both nutritionally and economically. We understand that it is still being evaluated but that it not thus far achieved great success. This illustrates the fact that any change or modification has to account for the cultural aspects of the country, and that when they are considered, the possibility of success increases.
Food Production and Technical Issues
Food as a Business. Ultimately, the production of foods and ingredients is the responsibility of the manufacturer. They must work with the regulators, address consumer pressures and meet the demands of the buyers. Those operating food processing plants in developing nations not only are producing foods, but they are running a business. To encourage them to change and to upgrade operations so that they operate safe and sanitary facilities, agencies or individuals who work with these companies need to understand this basic premise. If these operators can see that implementing a HACCP plan or adopting Good Agricultural Practices (GAPs) will increase their business, then there is a good chance that they will be willing to make the necessary changes. Recommendations to upgrade must, therefore, be couched in business language that these individuals can understand.
We previously addressed one issue that hinders many companies: one boss making all decisions. Managers must make a conscious decision to build an organization where they can trust their staff to make the right decisions that will maintain and build the business. A confident and enlightened manager will be more prone to do this if he or she has a pool of good people from which to draw. This underscores the importance of a good educational system that can provide ambitious and competent people to the industry.
Cooperation. A common problem in many developing nations is a lack of cooperation within the industry. As an example, the frozen vegetable processors in one nation may know one another personally, but consider the other companies solely as competitors, even though each company has the same technical, marketing and sales problems. The development and/or strengthening of industry trade associations are one means to address these common problems. These groups require strong, honest and ethical leaders, who have the ability to garner the trust of the member companies and who are personally committed to building the association. Trust is the real key. If the association inspires trust, the chance that the member companies (and competitors) will work together is enhanced.
Once companies begin to work together, individual problems become association issues and may be addressed as such. The association can organize the necessary educational programs in prerequisites and HACCP, and even work to develop industry models that will allow individual companies to develop and implement the programs. For example, rather than pouring money into an existing association, which all too often goes for fancy offices, members should identify potential association leaders and use that money to educate them. Have them work as paid interns in similar associations in the U.S. or Europe, or give them the opportunity to visit and work with a cross-section of associations in developed countries.
Using Information. It has been said that information is power, yet most food processors in developing nations fail to capitalize on information that is already in their hands. There is a real need to collate and analyze information that already resides within a company's files. All too often, the quality group diligently tests and then files that data away. If a product is "out of specification," the company will take immediate action, but the filed data is ignored. In industry, we have observed the same situation discussed earlier with regard to the regulatory agencies: failure to build databases. We urge food processors to take advantage of their dusty files and get that information into a computerized database that will allow it to be analyzed and used. This should not be an expensive proposition, especially when one considers that many young people are quite computer literate. Hire staff to develop a database and enter the old data. This information will become a valuable tool when the time comes for developing and implementing a HACCP plan.
As an example, if your HACCP team expresses a concern that an ingredient or product from an individual supplier poses a risk, the new database may provide an answer. Or, the discussions may focus on whether a point in the process should be made a critical control point (CCP). The database might provide information that can answer that question. It could also be used to modify an existing HACCP plan. An analysis of the data during a yearly validation exercise may show that a CCP could be eliminated. Finally, if hard copy files can be put into an electronic database, the processor not only will be able to more easily access information, but unneeded records can be disposed.
HACCP Prerequisites. We have mentioned that one of the greatest problems in developing nations is the weakness of HACCP prerequisite programs. Cleaning and sanitizing, pest control, preventive maintenance, sanitary design and other elements of these prerequisite programs are generally weak; so weak, in fact, that they often pose real safety risks.
There are two basic problems that need to be addressed. The first, and most obvious, is that food processors need to learn about compliance with Good Manufacturing Practices (GMPs). Educational programs, in-plant audits and one-on-one sessions with the processors are the way to enhance compliance. The audits and one-on-one sessions should be part of a long-term program, whereby people who understand the sanitation and food safety work hand-in-hand with the companies to gain improvements. The mere act of coming in, doing an audit and making some suggestions is not going to accomplish much. Suggestions must be in writing and include ways to improve, Companies should also expect follow-up audits. Discussions of the costs and benefits of enhanced compliance should be part of the dialogue. Of course, the processor must have some incentive to improve. If the operation is selling product to buyers who really don't care about quality or safety, the chances that the company will wish to enhance its operations are significantly reduced.
The second problem is even more basic. In many developing nations, the food processing industry simply does not have access to the tools, supplies and services needed to develop the necessary prerequisite programs and a HACCP plan. For example, there are pest management companies in most developing nations, but they tend to be "trappers and sprayers," and not partners in building an integrated pest management program. Processors in developed countries sometimes do not realize how fortunate they are to have all the services and products they need, but also a choice of several different vendors. The food industries in developing nations would really benefit if an effort was made to develop the needed support structures. These needs range from pest management, cleaning and sanitizing, sanitary design and construction, to monitoring equipment and laboratory supplies.
There are several ways to address these deficiencies. Governments could offer tax benefits to established international companies to set up operations in their countries. Other options include creating internships in developed countries for people or companies who want to upgrade knowledge and capabilities. Government can finds ways to work with the industry to make sure that they understand that there are differences in service providers or vendors, specifically in understanding what such a provider, like a pest control operator, should provide so they can shop appropriately, and avoid simply basing their selection on price.
Why Sanitation is Important. Efforts also must be made to educate industry in developing nations about the importance of basic programs like sanitation. The lack of pest management and sanitation programs in these nations is all too obvious if one goes to the FDA website and looks at the origin of products that have been embargoed. Many processors in these nations seem more concerned about finding a magic bullet that will clean up finished product rather than build sanitation into the process.
What Developed Nations Need to Do
Developed nations have a stake in what goes on in developing countries, and they know it. There have been millions of dollars poured into the developing world, yet has all this been effective? In the area of food safety, the results have been mixed. We would suggest that supporters in the developed countries take a step back and rethink the results of their efforts.
The first issue that should be addressed is coordination within a country. Providing aid to developing countries is noble, but the donor nations need to coordinate their efforts. It makes no sense to send a consultant to teach a HACCP workshop if there are no plans to address basic prerequisite programs. One or more of the donor nations operating within a country need to take the lead and bring their colleagues together to plan and organize a systematic and long-range program that addresses food hygiene and food safety. These technical programs must be accompanied by demonstrations as to why good sanitation, GMPs and development of and implementation of sanitation standard operating procedures (SSOPs) make good business sense. They must include efforts to strengthen the support industries such as those that supply packaging, pest management services, cleaners and sanitizers, monitoring equipment, laboratory supplies and all the products and services that are needed to grow a food business. We acknowledge that there will be companies, usually those with an ongoing relationship with a multinational, who are ahead of the curve and can handle more advanced programs. These companies should be used as examples to others and efforts should be made to get their people involved as instructors.
To encourage companies to upgrade, programs such as the Commodity Import Program (COP) administered by the U.S. Agency for International Development are an excellent idea. This program allows processors to purchase equipment from the U.S. at reduced costs by waiving interest for set periods. Other nations have similar programs for equipment. We strongly suggest establishing similar programs that will allow the food industry to access such support. Rather than limit such programs to capital equipment, we also suggest expanding it to include disposables and ingredients.
Companies that get involved with carrying out the projects funded by the donor agencies need to refocus their efforts on their true clients, the food industry. Often, these contractors and their consultants simply look to the agency that is funding them. They write massive reports to the contractor that are often never seen or are of little value to the industry. These contractors need to work with and support the industry honestly and with integrity. If this path is followed, there is a good chance that the results will be positive and beneficial. If the industry is happy, the contractor should be happy.
If programs aimed at enhancing food safety in developing nations are to be successful, the keys to success are long-term commitment to the food industry and to the people working within that industry. Long-term commitment by developed nations is important, because it gives individual companies and the industry the confidence that support will be there if and when they make the commitment to improve. This is especially important where HACCP is concerned. A comprehensive series of workshops addressing prerequisites to HACCP will take time to plan and organize. It would be advisable to repeat the programs several times to allow the industry "grapevine" to help with marketing. Make sure that instructors are people who have worked in the industry and understand practical problems and their solutions. Industry people do not want to hear theory, but practice.
It may be a year or more before a decision is made to offer a HACCP workshop. Instructors and consultants must also be given a chance to work with the industry. They should visit as many plants as possible to get a feel for the "state of industry" and the problems they face. After each visit, consultants shouldsend the company a detailed report of observations and recommendations. We have found that criticism is accepted if solutions are included, especially if the consultant can offer different means to address a problem.
Finally, when looking for consultants to work in developing nations, seek out people who really care about helping others do better. Find people who take pride in a job well done and who want to leave a mark. Processors with whom we have worked know who cares and who is there to "collect a paycheck." Look for people with vision and who have kept up with new technologies, new systems and new methods of instruction. These professionals should have the creativity and the understanding that what works in one country or one part of the world, may not work in another.
Cooperation is Key
The food processing industry in developing countries face an uphill battle when it comes to developing and implementing the systems for safe and wholesome foods. There are problems with the government, the educational systems, the culture and how things are done in the plants. We have offered a few ideas for helping these nations overcome these constraints. Unfortunately, there are so many issues that need to be addressed that the simple act of taking care of one may unveil two or more problems.
Developed nations need to work together to address the problems in developing nations. Governments must work together to build trust and strengthen the agencies regulating the industry. Work with industry must focus not only on helping them upgrade operations, but also must fully demonstrate why sanitation and food safety are good business. Above all, developed nations need to help the stakeholders in developing nations build trust and cooperation. Industry, academia and government need to work hand-in-hand for the good of their nation. Without cooperation, change will take much, much longer.
Richard F. Stier is a consulting food scientist based in Sonoma, CA. Formerly the Director, Technical Services for The Competitiveness Initiative-Mongolia and consultant with the Agricultural Led Export Business project based in Cairo, Egypt, Stier has international experience in food safety, food plant sanitation, quality systems, process optimization, GMP compliance and food microbiology. He has worked with a wide range of processing systems and products, including canning, freezing, dehydration, deep-fat frying, aseptic systems and seafood processing. Prior to joining these projects, he worked as an independent consulting food scientist, which allowed him to work with clients in Europe, Asia, Africa, Mexico and the U.S.. Stier's professional experience also includes positions as Director of Quality Assurance for Dole Packaged Foods North American operations, and with the National Food Processors Association, where he served Manager of the Microbiology Section for The National Food Laboratory. He recently served as the councilor representative to the IFT Executive Committee, where he has helped to develop the association's international programs. He isurrently is a member of the IFT's Committee on Global Interests. He can be reached at rickstier4@aol.com.
Morad Ahmed has more than 30 years of experience in the international food industry, including positions at seafood and frozen food companies in Egypt and Switzerland. From 1994-2002, he served as the technical co-director of the ALEB-USAID project. He also worked with the Norwegian Trade Center in Alexandria, Egypt for a decade.
Herbert Weinstein, Ph.D., has more than 30 years of industrial experience working with food companies such as General Foods and Unilever in most technical aspects of food manufacturing, distribution, logistics, product development, quality control, quality assurance and management. Weinstein has worked in fortification projects in several countries in Latin America, Middle East and in Africa. His expertise is in the areas of technical feasibility, quality control and assurance, analytical/manufacturing training, monitoring and control, product development and stability testing, as well as a legislation and liaison function between private and public sectors.
Looking for a reprint of this article?
From high-res PDFs to custom plaques, order your copy today!