Pest Management: Inside and Out
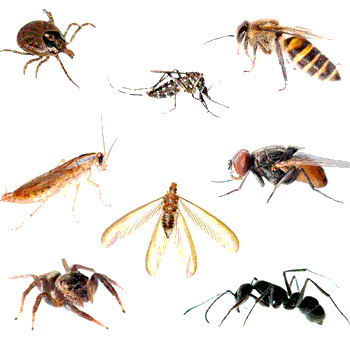
Insects are the most plentiful group of all the animals on earth. Approximately 80 percent of the worlds known animal species are insects. The house mouse and the Norway rat are the most successful mammals on earth next to man. It is not surprising that these animals place constant pressure on our food facilities, especially during the warmer seasons of the year. They can enter from the environment surrounding the structure; come in with delivered goods and if sanitation and structural conditions are not in line, become established in the building.
There are three lines of defense a food processer can use in preventing pests. These include protecting the exterior of the facility, inspection of incoming goods and interior pest prevention.
Protecting the Exterior
The first line of defense takes place around the perimeter walls and at the utility penetrations into the structure. It is important to take steps to reduce conditions that will attract pests to the facility like lights and food spills. Exclusion is the next concern. Make sure all doors, vents, windows and other building penetrations are well sealed. Some of the key procedures for a food processor to utilize on the exterior are as follows:
• Make sure all exterior doors seal well when closed and employees keep doors closed when they are not in use. If doors need to be opened for ventilation purposes, use screens. There are a variety of screens available for dock doors.
• Make sure dock bumper guards seal effectively around the trailer backed up to an open dock door. Insects and even birds can enter through these spaces. The most common gap is at the base. Saddle type bags can assist in sealing this area. In addition to brushes, door sprags can be used at the base of doors to help seal gaps at the dock plates. Sometimes, air curtains can be used to supplement other preventative methods. This can be especially important in areas where smaller delivery trucks are used.
• Quick roll up doors can be another line of defense used to separate sensitive areas from receiving areas. This is one more barrier for flying pests to get through.
• Many insects are attracted to lights, and proper light management can help assist in reducing the number of flying insects entering the building. Use sodium vapor lighting versus mercury vapor lighting whenever possible. Mount lights 150 feet or more from the building and direct towards the building instead of wall mounted units, if possible. Use motion light sensors to turn lights on and off when appropriate and consider the use of light filtering films on windows to reduce light emissions from the interior.
• Negative air pressure can be a major concern in facilities. The simple act of opening a door can permit the entry of insects as they are carried into the building on air currents. Although expensive, sometimes changing the pressure rating of the structure may be the ultimate answer in some pest situations. Air curtains or fans may help but it will depend on the level of pressure present and whether or not the air curtain can compensate sufficiently.
• Maintain a vegetation free barrier around the immediate perimeter of the structure (Photo 1). Select other landscaping materials which are less attractive to pests. Flowering and fruit producing plants are less desirable. Avoid low growing plants that hide soil and may encourage burrowing rodents. Use gravel barriers instead of mulch.
• Keep food spills to a minimum, especially around dumpster compactor areas and bulk unloading areas. Do not overlook roof areas since product spills and accumulations can occur here. Another area of concern can be trailers which are used for holding product that is going to animal feed. These trailers should be well sealed and inspected and cleaned prior to returning from feed delivery sites. These drop-off sites can be farms or other areas where sanitation and pest management programs may not be at the same level as the food facility.
• Do not store pallets on the exterior of the structure since they will be exposed to pests and pests can be transported inside with these items.
Inspection of Incoming Goods
The second line of defense is the inspection of incoming goods. Food processors should have a detailed program in place and train their employees regarding proper inspections and rejection of shipments. Mice in particular can come in on product and go undetected for long periods of time. They can obtain the water they need from the food they are eating and may not leave the pallet. The inspection of palleted product is critical to early detection (Photo 2). Food plant staff should check the shrink wrap, product, between product stacks and the pallet. Wood boring beetles, carpenter ants and psocids can be associated with wooden pallets. Recycled pallets can be more prone to problems since they travel from site to site, and may be contaminated with foods not normally associated with a particular processor.
Care for the Interior of the Plant
The last line of defense is the interior of the plant itself. It is important to establish a thorough cleaning schedule for all areas. The hard to clean areas are the locations most prone to pest problems. These include overhead pipes, duct work, false ceilings and electrical panels, especially in dry processing facilities (Photo 3). Equipment requiring lock out / tag out or confined space entry permits are often difficult to access for routine inspection and cleaning and therefore can be locations where pests commonly prosper.
Inventory management is another key interior pest prevention component. Using the first in/first out system of stock rotation is critical. The longer a food product remains in inventory, the more susceptible to stored product pests it becomes. The tracking of product set for rework and partially open stock is also important. Always use the first in/first out system of stock rotation whether it is ingredients, finished product, open product or rework.
Traps and monitoring devices should be used indoors to help monitor the effectiveness of the defense lines. Insect light traps, pheromone traps and rodent traps are common examples of these monitoring tools. A frequent inspection of critical areas is also required. Occasionally, pesticides may be needed when the proactive defense system fails.
Contamination of food products can be costly to food processors in a variety of ways. Being proactive in prevention can take effort but is essential in food safety and retaining consumer confidence. All three lines of defense should be utilized with special emphasis on stopping pests at the door.
Patricia Hottel is technical director at McCloud Services, based in South Elgin, IL. For more information, please visit www.mccloudservices.com.
Looking for a reprint of this article?
From high-res PDFs to custom plaques, order your copy today!