Single-Step Acid Wash Cleaner to Improve Cleaning Efficiency
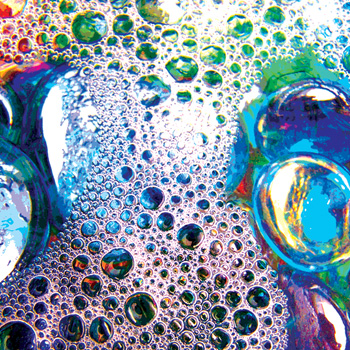
One-Step Acid™ (OSA) is a new patented detergent manufactured by DeLaval Cleaning Solutions designed to improve clean-in-place (CIP) cleaning efficiency by combining the alkaline detergent and acid cycles into one cleaning step. This low foam detergent lifts and removes organic soils, such as fats and proteins, while preventing and removing hard water scale. The convenience of single cycle cleaning decreases the amount of CIP cycle time required for a manufacturing facility thereby saving water, energy and reducing chemical discharge.
Background
As part of our vision of making sustainable food production possible, DeLaval Cleaning Solutions has designed a line of cycle time-reduction cleaners. OSA is an integral part of this line. It contains a proprietary and patented blend of surfactants and acids designed to both clean and de-scale cold processed surfaces.
Traditional CIP cleaning programs typically include four key cycles: pre-rinse, alkaline wash, acid wash (optional) and sanitize. In order for a surface to be properly cleaned, a prerequisite for effective sanitizing, both organic and inorganic soils must be removed during the wash cycles. Gross particle removal is accomplished during the pre-rinse cycle. This allows for the next two wash cycles to better access the surface to be cleaned. Removal of organic soils is accomplished with an alkaline detergent, usually chlorinated, while removal of inorganic deposits (hard water minerals) is accomplished by an acid solution.
OSA Chemistry
OSA is intended to replace traditional chlorinated CIP cleaners and allow customers to combine the alkaline and acid cycles into one wash step. The purpose of the traditional alkaline wash cycle is to break up, lift and remove solids such as proteins and fats from a surface. Replacement of the alkaline wash with OSA is possible because of its unique blend of low—foaming surfactants and acids. The unique blend of acids in OSA, with the aid of the surfactants mentioned above, allow for highly efficient solubilization and consequent removal of mineral deposits. OSA contains both organic and inorganic acids. The blend of organic acids and mineral acids in the formulation provides strong acidity with improved penetration and solubilization of organic soils, while reducing potential corrosion problems. This greatly improves cleaning which is not common for typical descaling acid products. Additionally, the acids in OSA are able to remove calcium carbonate and other low solubility salts that are present in hard water and would precipitate in alkaline cleaning routines. These acids are also highly soluble in water, thus reducing the likeliness of any chemical deposits after the cleaning cycle.
The surfactant blend in OSA is optimized to lift and solubilize fatty and protein soils. A surfactant is an organic molecule with hydrophobic (water-repellent) and hydrophilic (water-loving) ends. It may also have a net charge (either positive or negative). Both of these characteristics allow the surfactants to attract and emulsify organic molecules, such as fats, present on surfaces (Figure 1). This physical trapping of the soil lifts it from the surface and keeps it suspended in a solution, allowing it to be washed away as the detergent is circulated through the pipes, without re-depositing on the surface. Additionally, breaking hard water deposits, by the acids in the formula, also increases accessibility to organic soil deposits. Properties for OSA are given in Table 1 for the concentrate and several typical dilutions.
In Vitro Cleaning Studies
The cleaning efficacy of OSA was first assessed under controlled conditions in vitro under a range of conditions. In vitro testing of OSA at its lowest recommended use dilution (0.5 oz/gal) shows comparable removal of milk soils even in the presence of 300 ppm (17.5 grains/gal) of calcium carbonate (CaCO3) vs. a commercial chlorinated alkaline formula (Table 2).
Materials Compatibility
In addition to exhibiting cleaning efficacy, detergent products are required to be compatible with a range of materials that they will contact during the cleaning process. As mentioned before, organic acids have lower corrosion on metal surfaces than their inorganic counterparts or than chlorinated detergents. Our studies have reported the absence of corrosion on stainless steel or rubber deterioration at recommended use concentrations (Table 3). Its high compatibility with common materials used in food processing facilities makes OSA suitable for adequately cleaning delicate and intricate cold process surfaces without any damage to the surface. OSA applications include most systems currently being cleaned with traditional chlorinated alkaline CIP systems cleaning both raw and pasteurized product equipment. As with any strong acid, OSA must not be used to clean soft metals such as aluminum or other alloys.
Field Trials
OSA was specifically designed for milk-based soils. In the milk industry, OSA has not only saved customers time, money and water but has also lessened their environmental impact by reducing chemical consumption, minimizing impact on the waste water system and in many cases, eliminating the use of chlorine.
Trial 1.
• Type of producer: Milk processor.
• Equipment Cleaned: Multiple CIP systems—raw and pasteurized silos, tanks and lines
• Products: Whole milk, cream, condensed skim, permeate, protein, lactose
• 100 cleaning cycles per day
• OSA dose: 4 weeks at 1% (v/v) followed by 4 weeks at 0.5% v/v
• Product being replaced: chlorinated alkaline detergent
• Results:
• Replacement of two chemical feed pumps for one
• Eliminated use of chlorine
• Less water needed for rinsing
• Reduced scale buildup in CIP wash tanks (Figure 2)
• Soil holding ability of the OSA is very good; 3,000-gal wash tank prior to OSA was drained every 3 to 4 days; while using OSA wash tank was able to be drained every 8 days; drained solution was clear without heavy soil load
• No issues with foam were noted
• The wash and rinse CIP times were successfully reduced from 15 min to 9 min, saving both time (6 min/cycle) and water (360 gal/cycle)
• Time effect – 6 min × 100 cycles = a savings of 10 hours of CIP time/day
• Water effect – 360 gal × 100 cycles = a savings of 36,000 gals of water/day
• Impact of effluent in waste water system was diminished by the elimination of chlorine as well as the reduction in amount of daily effluent
• Added benefit: plant was considering adding a new CIP system due to current cleaning time restrictions; by freeing up the additional 10 hours using OSA, this was no longer necessary; resulted in substantial capital savings
• Recommendation to continue use at 0.5% OSA
• Usage of OSA results in a cleaner surface, as determined via ATP testing, vs. a conventional chlorinated CIP cleaner (Figure 3)
In addition to its excellent performance on milk soils, the use of OSA is also highly advantageous in other industries. For example, breweries commonly use 1–1.5% caustic in their cleaning regimen and do not use an acid rinse. Up to 1% of caustic concentration reacts with the CO2 present in the tank, losing both caustic for cleaning and CO2 for processing. The use of OSA in brewery tanks will be advantageous as it will not react with CO2. Advantages include:
• Saving CO2
• Shorter turn-around time
• Less water needed for rinsing
• Lower temperatures for wash
Thus, OSA can provide a more efficient and effective cleaning than current regimens while allowing the CO2 to remain in the vessel.
Economics of OSA
A comparison of a typical Alkaline wash, Acid wash and sanitizing cycle vs. an OSA cycle is outlined in (Table 4). By combining the alkaline wash and the acid wash into one step, the overall cycle time maybe shortened 30 to 60 min. In general, the chemical, water and energy savings amount to approximately $50 per CIP circuit per day for a 7-day operation. Total savings depend on the volume of each circuit, the cost of chemicals being replaced, energy costs and the cost for operational hours saved. Table 5 and Figure 4 show an example of the expected annual savings for a 150-gal circuit.A comparison of a typical alkaline wash, rinse and sanitizing cycle vs. an OSA cycle is outlined in (Table 6).
By replacing the alkaline wash, rinse and sanitizing cycle vs. an OSA, rinse and sanitize cycle the overall cycle time maybe shortened 5 to 10 min. In general, the chemical, water and energy savings amount to approximately $10 per CIP circuit per day for a 7-day operation. Total savings depend on the volume of each circuit, the cost of chemicals being replaced, energy costs and the cost for operational hours saved. Table 7 and Figure 5 show an example of the expected annual savings for a 100-gal circuit.
While the time for either wash step may remain the same, the need for an additional acid wash step maybe eliminated, and the rinse time after the alkaline wash step maybe reduced. On average, the implication is a reduction in the overall cleaning cycle, added benefit of reduced chemical exposure, presence of less chemical holding tanks and improved wastewater management efficiency.
Benefits also extend to a reduction in water usage. Assuming 100–300 gallons during each rinse or wash cycle in pipeline CIP systems, elimination of 2 of the steps in the overall wash cycle are equivalent to savings of 200–600 gal of water per circuit per day.
Furthermore, the recommended use temperature of OSA is 50–60 °C (120–140 °F), this in contrast to standard alkaline wash temperatures of 60–70 °C (140–160 °F). In fact, excellent performance of OSA has been observed at temperatures as low as 40 °C (100 °F), with the added benefit of little to no foaming during CIP. Lower temperatures are not recommended as they may cause fats to redeposit onto other surfaces. Every 10-degree reduction in water temperature translates to an approximate energy savings of 158.8 kJ/gal of water, or up to 40 kWh/CIP circuit.
Finally, by leaving a cleaner surface, OSA enhances acid sanitizer performance. The active ingredients in sanitizer formulations are typically highly reactive molecules that “attack” any organic deposits on a surface. Additonally, the presence of certain minerals, can affect their activity by either a chemical interaction or by physically hindering their ability to reach microorganisms present on the surface. Thus, the presence of soil residues can negatively affect the ability of a sanitizer to reduce the viable number of microorganisms on a surface. A cleaner surface is sanitized more efficiently, resulting in higher production quality.
A summary of the savings provided for the different CIP programs and cycles can be found in Table 5 and Figure 4, and Table 7 and Figure 5, respectively.
Conclusions
By reducing or eliminating an additional wash and rinse step, your food processing plant’s cleaning time, water, energy and chemical use are minimized and cleaning capacity is maximized. Reduced cleaning time through the use of OSA translates into more available processing time. In some cases, the amount of cleaning time necessary maybe reduced to such a level that the need for capital investments for additional CIP equipment might be avoided. Additionally, water and chemical discharges are reduced, both of which translate into a more sustainable production process with less environmental impact. Finally, the work of the cleanup crew can be better utilized by eliminating steps, eliminating the need for overdosing chlorinated cleaners to compensate for chlorine loss and providing a cleaner surface that improves the performance of acid sanitizers.
These benefits not only result in monetary savings but also positively impact the quality of the final product as well as the safety and morale of the employees.
Looking for a reprint of this article?
From high-res PDFs to custom plaques, order your copy today!