LIGHTNING MVP ICON™: Rapid Solution for Environmental Monitoring
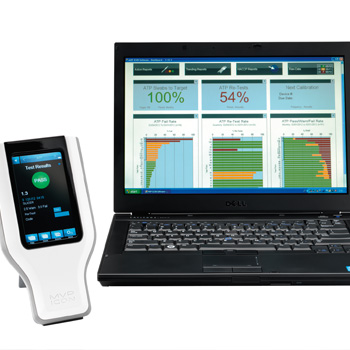
With the recent introduction of the Food Safety Modernization Act (FSMA), regulatory guidelines for controlling food hazards have become increasingly more stringent. For food manufacturers, ensuring products are free from potentially hazardous elements such as pathogenic bacteria often starts with ensuring these organisms are not present in the manufacturing environment or equipment. In fact, FSMA requires that manufacturers diligently establish, evaluate and document preventative controls and their efficacy to ensure a safe production environment. This can best be accomplished through the implementation of a comprehensive environmental monitoring program, including elements of all of the following methods.
Targeted Pathogen Detection: The most specific method is direct pathogen detection. Product contamination with pathogens frequently occurs after processing through contact with environmental surfaces. As such, a primary concern for most food manufacturers is preventing the establishment of these organisms anywhere in the plant. While highly targeted to detect specific organisms such as Listeria or Salmonella that present a public health risk, these methods require one to five days after sampling to provide results.
Quantifying Microbial Levels: Plate count methods, either traditional agar or rapid methods, provide a quantitative estimate of key indicator organisms, such as total aerobic bacteria, yeasts and molds or coliforms. Tracking these counts provides a view into a sanitation program’s ability to control the microbiological population of the manufacturing environment. While impossible to eliminate, keeping the population relatively low reduces the likelihood of pathogens becoming established. Similar to pathogen detection methods, these results are available in one to five days after sampling.
ATP Detection: Ensuring proper cleaning and sanitation of the environment and equipment upfront is a critical step in controlling the microbiological population in the plant and preventing the establishment of pathogens in the environment. Adenosine triphosphate (ATP) is present in all living organisms and most foods, making it an ideal candidate for environmental testing methods targeting both microorganisms and food residues. ATP is easily detected and, while the source of the ATP cannot be determined, the level of ATP present on a surface is a direct indicator of the cleanliness of the surface. Additionally, ATP test results are available instantly, allowing problem areas to be addressed immediately. Trending ATP levels over time can help improve the effectiveness of any sanitation program.
An innovative new tool from BioControl Systems that monitors ATP levels and helps manage a company’s sanitation program is the LIGHTNING MVP ICON™ and Dashboard software. The MVP ICON and Dashboard software was developed to help food manufacturers manage their sanitation programs and comply with Hazard Analysis and Critical Control Points (HACCP) and FSMA requirements, as well as their own internal Sanitation Standard Operating Procedures (SSOPs). Quality teams can utilize the software’s program management capabilities to proactively monitor key performance indicators and perform trending analysis to evaluate whether cleaning and sanitation efforts are effective. The innovative dashboard interface provides insight into vital criteria for HACCP and hygiene monitoring programs, such as automatic identification of problem areas within the facility, whether failed results have been re-cleaned and re-tested and if the appropriate number of samples have been tested. In-depth analysis and reporting capabilities reveal if a sanitation program has improved over time or where vulnerabilities lie to proactively improve cleaning procedures. These enhanced reporting capabilities, along with the advanced design of the new MVP ICON instrument, have made it the go-to system for many food manufacturers.
When asked to describe their experiences with the MVP ICON, a quality control professional from a leading U.S. ingredient manufacturer states, “The MVP ICON has been a huge asset to our facilities. When we incorporated the MVP ICON into our program, our employees had a first-hand view of how it works and how quickly the results become available. It has also made them even more aware of our cleaning processes and why it is important to follow them.” This newly designed piece of equipment utilizes the latest advancements in technology to provide a simplified user interface and smaller, lightweight instrument. Featuring the ability to randomize test points, create customized sample plans and track the re-cleaning and re-testing of failed test points, it is the ideal tool for ensuring clean surfaces before beginning production.
A successful environmental monitoring program incorporates a comprehensive, multi-tiered approach to maintaining a low-risk manufacturing environment. Targeted pathogen detection, quantification of key groups of indicator organisms and rapid ATP detection to determine surface cleanliness combine to reduce the potential risk of product contamination in a manufacturing facility.
To learn more about the MVP ICON as a rapid method for environmental monitoring, please contact BioControl at 800.245.0113 or email us at info@biocontrolsys.com.
www.biocontrolsys.com
Looking for a reprint of this article?
From high-res PDFs to custom plaques, order your copy today!