Planning for a Recall
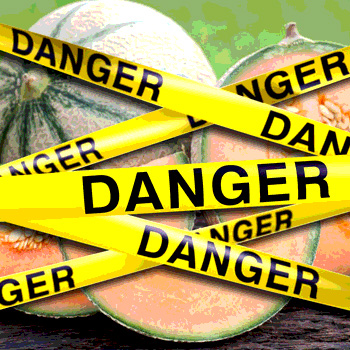
There may be no word that strikes greater fear in the hearts of individuals in the food industry than “recall.” Mere consideration of the term may mean that someone has been made ill or possibly died from consumption of or exposure to a food product. The response must be inordinately fast. You will be coordinating with government agencies, such as the U.S. Food and Drug Administration (FDA), the U.S. Centers for Disease Control and Prevention (CDC), state governmental agencies as well as other companies who sit both upstream and downstream of your position in the distribution chain of the food product at issue. The aftermath can leave injured consumers and damaged or destroyed reputations. The monetary costs may include lost profits, recall expenses, civil damages and potential criminal action. Despite excellent quality control, you may find yourself swept into a recall. Advance planning for recalls can save lives and can make the difference in the survival of your company.
Recalls may be conducted on a company’s own initiative, by FDA request or by FDA order under statutory authority. Recalls are utilized to protect consumers (both human and animal) from products which pose a risk of injury or gross deception or are otherwise defective. In the most serious of circumstances, manufacturers are required to report to the FDA’s reportable food registry within 24 hours of learning that a food presents a reasonable probability that the use of, or exposure to, such article of food will cause serious adverse health consequences or death to humans or animals (Class I Recall). Where the probability becomes more remote and/or the potential impact less severe, the required response time may be somewhat longer, moving from hours to days (Class II Recall).
While a written recall plan has long been a regulatory requirement, planning for a recall should include much more than a template form in a file. Recall planning should include record-keeping steps to be taken well in advance of any concerns but which will make any recall effort more effective. A team of advisors who will serve in various roles in the planning, execution and post-recall process is as necessity. And the requirements of a detailed written recall plan are being further clarified under the Food Safety Modernization Act (FSMA).
Recordkeeping Steps
Even where no significant risk has been identified, meaningful record-keeping procedures and maintenance of particular data will make recall efforts easier and more accurate. FDA guidance has itemized documents and data which they will want to see in a Recall Submission once a recall decision is made. Maintaining this information on an ongoing basis will make the collection process simpler. Recall Submissions ask for product information such as brand and generic names, model and catalog numbers, order numbers, product and packaging physical descriptions, intended uses, shelf life, copies of all labeling, inserts and directions. Submissions must also include various product codes such as lot or unit numbers, expiration dates, use by dates and universal product codes. Information regarding the volume of the recalled product must be provided including the total quantity produced, dates produced, quantity distributed and dates distributed. Additionally, information must be provided relating to distribution patterns such as the number of direct accounts sold to, geographic areas of distribution, a detailed list of consignees (including names, addresses, contact names, phone numbers) and information on both “ship to” customers and “bill to” customers. Although this does not represent all the information which must be submitted to FDA in a Recall Submission, it includes data and information which could be a part of regular record keeping procedures.
To take a more progressive approach, it is recommended that you also review the Pilot Project for Improving Product Tracing along the Food Supply System Final Report prepared by the Institute of Food Technologists at the request of FDA. Public comment is still open on the recommendations in that final report, but those recommendations should be considered in developing a record-keeping policy which will facilitate potential recall obligations.
Team of Advisors
Trying to identify trusted advisors to guide a company through the recall shouldn’t begin during the 24 hours during which notice is to be given for a Class I Recall. Your team may include various disciplines and individuals, some of whom may already exist within your company. A quality control employee with knowledge of the companies’ manufacturing processes and ability to test for possible contaminants should be included. An employee with knowledge of purchasing and distribution can advise of connections to suppliers, distributors and end-users who may have declared possible contaminants.
From outside your firm, consider an attorney with FDA experience who can provide you with advice as to whether a report to the food registry or whether a recall is appropriate. This person will also be immensely helpful in walking you through the process of coordinating with FDA. Next, a public relations consultant is critical to minimizing the long term repercussions of the entire recall process. They can assist with formulating the message you want to convey to confirm that all appropriate steps are being taken to protect the public. Their goal is to preserve the brand for the success of the company after the termination of the recall. Finally, from a risk management perspective, a litigation attorney should be involved to work closely with the FDA advisor and the public relation advisor. The litigation advisor may play a small part initially, but will review what the other advisors are doing with an eye toward how the response to the prospective danger, responses made to FDA and public relations statements will play to a jury, should it come to that. The wording of a script written to be provided to consumers who call the company with questions may appear factually accurate to your advisor dealing with FDA, not supportive of your message to the public relations advisor and constitute a statement that can be used as an admission of fault to the litigation advisor.
Written Recall Plans
Written recall plans have long been required under the Federal Food, Drug and Cosmetic Act. This has been re-emphasized under the proposed regulations in FSMA. Under both the Hazard Analysis and Risk-Based Preventative Controls Rules for human food and animal food, a written food safety plan must include a written recall plan for any significant risk identified. The plan must at a minimum identify the steps to be taken, and assign responsibility for taking those steps, to perform the following actions as appropriate to the facility:
(1) Directly notify the direct consignees of the food being recalled, including how to return or dispose of the affected food
(2) Notify the public about any hazard presented by the food when appropriate to protect public health
(3) Conduct effectiveness checks to verify that the recall is carried out
(4) Appropriately dispose of recalled food (e.g., through reprocessing, reworking, diverting to a use that does not present a safety concern or destroying the food)
Verification steps must occur after the initial recall to determine the effectiveness of that first effort. There has been no indication that these rules relating to recalls will change when the final FSMA rules are published later in 2015.
Going through a recall can be one of the most difficult times a food company faces. But with prior planning, the process can move more smoothly and you can feel more confident that you are prepared to survive.
Kathy Hardee, Esq., is co-chair of the Food & Agriculture Industry Group at Polsinelli, PC, which is composed of a team of attorneys from every legal practice area and who each have a focused background in the food industry.
Looking for a reprint of this article?
From high-res PDFs to custom plaques, order your copy today!