May the Force (and Flow) Be With You: Importance of Flow in CIP
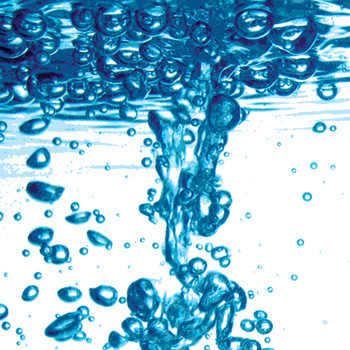
Often food producers are advised to change and/or increase clean-in-place (CIP) chemistry, time or temperature if a cleaning problem occurs in their process line (pipes, machines, tanks, etc.). Sometimes it works and sometimes it does not. The challenge is that to remove soils from a surface, CIP liquid (i.e., both for cleaning and disinfection) must reach the soil to have an effect. Studying the flow conditions during CIP can help to solve this challenge.
Flow of liquid is responsible for transporting energy (heat and chemistry) to the soil on a surface and also for providing the actual mechanism of lifting or dragging soil away from the surface. The alternative to changing and/or increasing CIP chemistry, time or temperature is to increase either transport of the chemistry and temperature already available or the force in problematic areas. Preferably, increased cleaning effects should be obtained without increasing the costs for power (i.e., increased volumetric flow rate) and thermal energy (i.e., increased temperature).
Examples illustrating the means of improving cleaning without increasing the overall volumetric flow rate for CIP are provided in this article, including oscillating volumetric flow rate and tank cleaning using rotary jet heads.
Cleaning is Simple to Describe
Cleaning can be described using a simple illustration: Sinner’s circle. It depicts that cleaning is a matter of applying chemistry and temperature and cleaning for a sufficient (contact) time to weaken the bond between the soil and the surface to allow the available force to remove the unwanted substance (soil) from the surface. Examples 1 and 2 describe the effect of these four parameters and highlight why force is an important parameter even though it is often overlooked when it comes to CIP.
Example 1: Two glasses (A and B) of milk have been emptied. A thin milk film is always present at the bottom of the glass. Glass A is cleaned immediately, while the milk film in glass B is allowed to dry onto the glass surface. Flushing water into glass A cleans the glass. The chemistry, temperature and time effect is extremely small and the force of the water removes the milk film. To illustrate the effect of the different parameters on cleaning, a sequence for cleaning glass B is described. Initially, a brush is applied to the milk film to try to physically remove the film (not possible). Second, cold detergent is put into the glass and given time to loosen the soil from the surface. Then a brush is applied to try to remove the milk film (still not possible). Finally, hot detergent is put into the glass and given time to loosen the soil from the surface. It can then be removed by the brush; the detergent and heat have loosened the soil sufficiently for the applied force to remove the milk film.
Example 2: Milk heated in a pot burns onto the bottom of the pot—a fouling layer has been generated. To remove the fouling layer, cold detergent is put into the pot. A brush is used to try to remove the fouling layer from the surface. Only small parts of the upper fouling layer are removed by the force applied. This is because coherent forces (which hold the fouling layer together) are smaller than the adhesive forces (between the fouling layer and the bottom of the pot). Now, the heat is turned on and the temperature of the detergent increases. If you wait long enough, the soil might loosen due to the natural convection of the water. However, after much less time, you will be able to remove the soil from the surface by a soft touch of the brush.
Examples 1 and 2 show that all four parameters are needed to perform a cleaning task. Temperature, chemistry and time can do a lot, but without force, soil is not removed from the surface. Temperature, chemistry and time loosen the soil from the surface until the adhesive force is less than the force present at the soil/CIP liquid interface. For cleaning out of place, physical contact can be used to generate a relatively high force. For cleaning in place, the movement of the liquid inside the equipment generates the force—this is a relatively low force (at 1.5 m/s in a 2-inch pipe, it is approximately three orders of magnitude less than that of a cloth on a surface).
The four parameters can be looked upon as energy contributions. For light soiling, the sum of the energy is smaller (e.g., fresh milk film in a glass) than for heavier soiling (e.g., soiled pot). All four parameters must be present for cleaning to take place. The level of these parameters needed for cleaning can be high or low depending on the nature of the soil, the soiling conditions and the surface topography.
From the above, it should be evident that chemistry and temperature must be in contact with the soil at specified levels for an expected contact time for a given force to clean the surface. The way to transfer chemistry and temperature to the soil is by the mechanism of flow inside the equipment (process line). If flow is not present, then transport of chemistry and temperature can only be done from conductive mass and heat transfer; while in a flowing environment, mass and heat transfer are convective. This also explains why turbulent flow should be present during cleaning throughout the process line (mass and heat transfer increase from Re = 1,000 to Re = 10,000). However, local flow conditions can result in zones with low turbulence.
In closed processing lines, it is well known that for cleaning of surfaces exposed to velocities above 1.5 m/s, the right chemistry, temperature and cleaning time make the surfaces relatively easy to clean. Some of the most difficult areas to clean are dead-ends, shadow zones and crevices. The force is very low in certain parts of these features and, to make matters worse, the mass and heat transfer are also very low in those places. This is a recipe for disaster. Increasing the concentration of chemicals in the CIP liquid does not help greatly unless the mass transfer to the problematic area is also increased. Increasing the volumetric flow rate only marginally increases the force in the areas that are difficult to clean.
In the following section we will look at how mass and heat transfer can be increased using the volumetric flow rate (without increasing the average volumetric flow rate during CIP) and how we can focus force with the volumetric flow rate available (and even by reducing the volumetric flow rate).
Increased Heat and Mass Transfer Using the Flow Rate
By now, it should be clear that heat and mass transfer are very important in CIP cleaning. Different approaches exist to increase the mass and heat transfer to a surface compared with mass and heat transfer for a stationary turbulent flow situation. These approaches include the following:
• A geometric design that generates flow and breaks down the boundary layer or a fully developed flow (e.g., a straight pipe) so that boundary layer build-up must start over. Examples of such designs are insertion of a winglet that generates swirl (disturbs boundary layer downstream of the device) and rods (shape arbitrary) in a cross-flow that generates von Karman vortices (i.e., disturbs the boundary layer downstream of the device).
• Variation in a cross-sectional area that results in three-dimensional swirl zones (e.g., a spherically shaped valve house or housing for a measuring probe) and disturbs overall heat and mass transfer in the zone.[1]
• A changed CIP procedure that breaks down the boundary layer, such as a stop-go-stop-go method that makes the flow inside the pipe come to a rest for short periods of time. When flow is restarted, the boundary layer must rebuild.
• A pulsating flow with a waviness greater than one that breaks down the boundary layer when the flow direction is reversed.
• Increased volumetric flow rate (also means increased costs).
One problem with many of the design features that promote heat and mass transfer is that they also introduce shadow areas when mounted in the flow. Hence, low wall-shear stress creates an additional difficult-to-clean zone. We will now focus on increasing the heat and mass transfer based on pulsating flow.
Previous studies[2, 3] have shown that pulsating flow in a processing line increases the cleaning rate. Current results are very promising when the so-called waviness is greater than one (reverse flow direction is needed in a short period of time). This is necessary to disrupt the boundary layer. Others4 have found that a pulsating flow in a uniform direction has only a small effect on cleanability. The problem here is that the boundary layer is not disturbed enough to allow increased mass and heat transfer. Also, the fact that pulsating flow does not change the location of the zones that are exposed to low wall-shear stresses (e.g., the rotating center of a recirculation zone) decreases the effect of pulsating flow.
Currently, the Technical University of Dresden and the Technical University of Braunschweig are collaborating to determine the challenges of implementing pulsating flows in process lines. Some of the questions being investigated are whether pulsating flows yield undesired effects on other components in the processing line and whether the pulsations can be achieved with current processing equipment or if additional investments are needed to obtain pulsating flow with waviness greater than or equal to one.
Focus the Force
The most obvious way to increase the force in a processing line cleaned by CIP is to increase the volumetric flow rate. This would also increase the heat and mass transfer, a combination that would increase the cleanability of most parts of a process line. However, areas most difficult to clean are always located in corners, dead-ends and crevices. Increasing the volumetric flow rate does not increase the wall-shear stress[4] or heat and mass transfer significantly in those areas. Also, increased volumetric flow rate means higher costs for cleaning.
So what can be done to increase the force acting on the soil on a surface? For an existing processing line, this is not easy to achieve. Examples that could be relevant for the future include the following:
• Ice-pigging: A volume of slush ice is pushed through the processing line by the CIP liquid.[5]
• Draining the processing line during CIP: When CIP is restarted, the air-water interface flushing through the processing line generates a larger force against the surfaces it flushes through.
• Injection of bubbles into the liquid: The bubbles in the flow generate local, high wall-shear stresses.
• Jet cleaning of tanks and pipelines: A water jet generates a high force that can be focused to a specific area.
The development in tank cleaning technology is a great example of how better cleaning can be obtained with a lower volumetric flow rate. Traditionally, tank cleaning was (and still is) done by filling up the tank with detergent, heating the detergent, dumping it all and hoping that the tank was cleaned (very little mechanical action was supplied). The next development in tank cleaning was static spray balls (SSBs), where the CIP liquid is gently sprayed on the tank surfaces (impact point is in the same location all the time). The CIP liquid freefalls down the tank wall and cleaning is mainly achieved by the soaking effect (coverage). To increase the force, rotating spray heads (RSHs) were introduced. Here, water is also sprayed on the surfaces, but instead of being distributed throughout the entire tank at the same time as the SSBs, the RSHs distribute the water in a rotating manner (impact areas are instationary). A number of water fans are discharged from the RSHs and, as they rotate, the water fans hit all around the tank circumference. This allows for a soaking-mechanical cleaning-soaking sequence during which the mechanical cleaning step has a greater force than the SSBs because the flow available is focused in the fan and not in a larger number of sprays. At the extreme, we can choose the rotating jet head (RJH). Here, the volumetric flow rate available is focused into a number of jets discharged from nozzles. The design of the machine moves the nozzles in a two-axis rotation, which allows the jets and their accompanying footprints to cover the entire tank in a number of cycles. The impact force and the mechanical force in the footprint are much higher than the force provided by an SSB or RSH. The wall shear stress in the footprint is at least 10 to 500 times higher than the wall shear stress of a freefalling film. With this huge increase in force, the chemistry and temperature are no longer the most important parameters in cleaning. Instead, force is the most important factor. Hence, cleaning time, chemistry and temperature can be reduced for most types of cleaning.
While tank cleaning technology cannot be directly transferred into pipe systems, future equipment designs and positioning of small jet devices in critical areas could be options for focusing the force from the available volumetric flow rate.
Conclusion
It is extremely important to keep in mind that cleaning does not just depend on one parameter; all four parameters are essential for cleaning and must be considered when a cleaning problem must be solved. Otherwise, efforts to solve the problem will have little effect. A larger effect can be achieved by looking at all four parameters at once. Force (and appropriate fluid mechanics) cannot do it alone; chemistry and temperature are also needed. However, chemistry cannot do it alone either. Over the last decade, more scientific knowledge on CIP has been achieved and, in the coming years, hopefully this will result in either innovative designs that are easier to CIP or innovative CIP procedures. For this to succeed, the traditional ways of thinking when it comes to CIP must be revised; for example, in tank cleaning, it is now possible to clean primarily using force instead of primarily “soaking” with a freefalling film.
Bo Boye Busk Jensen, Ph.D., has an M.Sc. in mechanical engineering with a focus on fluid mechanics and a Ph.D. in hygienic design using computational fluid dynamics. Bo was employed between 2002 and 2007 as an Assistant and Associate Professor in hygienic design and food processing technology. He currently holds a position as an R&D engineer at Alfa Laval Tank Equipment.
References
1. Jensen, B. B. B. and A. Friis. 2005. Predicting the cleanability of mix-proof valves by use of wall-shear stress. J Food Proc Eng 28:89-106.
2. Augustin, W. and M. Bohnet. 1999. Influence of pulsating flow on fouling behaviour. Proceedings of the Engineering Foundation Conference on Mitigation of Heat Exchanger Fouling and its Economic and Environmental Implications. Banff, Canada.
3. Gillham, C. R., P. J. Fryer, A. P. M. Hasting, and D. I. Wilson. 2000, Enhanced cleaning of whey protein soils using pulsed flows. J Food Eng 46:199-209.
4. Jensen B. B. B., M. Stenby, and D. F. Nielsen. 2007. Improving the cleaning effect by changing average velocity. Trends Food Sci Tech 18:s52-s63.
5. Quarini, G. L. 2002. Ice pigging to reduce and remove fouling and to achieve clean-in-place. Appl Thermal Eng 22:747-753.
Looking for a reprint of this article?
From high-res PDFs to custom plaques, order your copy today!