What Defines a Laboratory Quality System?
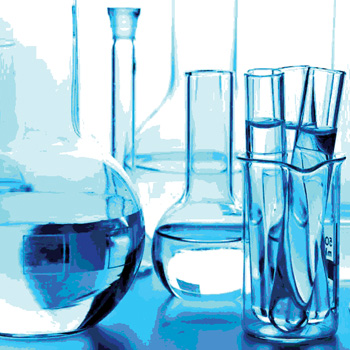
Quality is hard to define in a way that is appropriate for all situations. The term is usually used with products and services. As an objective characteristic, quality is not measurable but interpretable. In the testing laboratory, quality is interpreted as compliance with specifications. Therefore, quality means that the laboratory results meet the customer’s expectations and are accurate and defensible.
Historically, as production methods transitioned from individual producers to factories, mass production of goods incorporated automation and process control. Walter Shewhart was the inventor of statistical process control (SPC) and developed the Shewhart cycle. The cycle contains four continuous steps—plan, do, check and act (PDCA). With consistent utilization, the PDCA control circuit leads to continuous improvement. William Edwards Deming expanded on Shewhart’s ideas by defining a systematic approach for continuous improvement through constant evaluation and employee involvement that would improve production processes by setting and achieving increasingly higher standards. Within Europe and the U.S., the process of developing the quality management function within a company started in the early 1970s and is now close to maturity.
Management, Assurance and Control
Quality management works on the organizational level to implement an overall quality policy. A quality system refers to the organizational resources, processes and procedures to implement quality management, which is broader than both quality assurance (QA) and quality control (QC). However, a QA program is the backbone of the laboratory quality system. The relationship between the quality system, QA and QC is as shown in Figure 1. QA provides a management tool within the organization. In contractual settings, QA provides confidence to the customer. QC is a process within the QA program. The process is to collect evidence that the desired level of quality is achieved, and the process itself has no impact on the product quality.
Besides QA, the laboratory quality management system also includes management of equipment, supplies and inventories, management of capital, finances and budgeting, and providing training and continuous support of staff and customer service.
Essential Tools for QA
To ensure that the final laboratory results are correct, the QA program incorporates those planned and systematic laboratory activities that guarantee the accuracy and defensibility of testing results. The quality manual, Standard Operating Procedures (SOPs) and documentation are essential components of a QA program. The quality manual refers to the master document of the laboratory quality policy and serves as the primary resource for laboratory information. The management team is responsibile for ensuring adherence to the laboratory quality manual, QA plan and SOPs. Other supplementary records (e.g., instrument logbooks, reporting forms) are also critical components in a QA program. In the controlled environment of a testing laboratory, if the activity is not documented, then the activity never happened.
Besides thorough documentation of all procedures and processes, the laboratory also needs to choose the correct methods for testing and establish protocols to detect errors and initiate corrective actions. Validated methods are at the technical core of laboratory testing. To determine whether methods are fit for their intended purpose, the selected methods must have established accuracy, precision, calibration and limits of detection and quantification. For methods that are taken from a recognized resource, usually a verification process is sufficient to establish the method performance for the lab. However, if the analytical method is developed in-house, a full validation is required.
Audits are conducted to verify conformance to the requirements of the quality system. The audit is a tool to assess the effectiveness of the quality system and to identify places for future improvement in laboratory process and personnel performance. Internal audits need to be conducted at appropriate and practical intervals. Typically, the QA manager is responsible for performing the internal audits to address all elements of the quality management system, analytical activities, records and documentation. Auditing activities could include reviewing SOPs, worksheets, lab notebooks, balance calibration records, working control data, pipette calibration records, equipment monitoring logs and other related items for producing test results. The auditor typically uses a checklist to determine the auditing scope and content. The audit results then initiate corrective and/or preventive action to ensure continuous improvement of the quality system.
QC refers to a measuring process, or to check a result and provide assurance that all activities are performing within predetermined limits. One of the key QC processes in any laboratory is SPC, which utilizes statistical methods to evaluate variability in the laboratory testing and the stability of laboratory procedures. Control charts are the most commonly adopted tools to monitor the testing procedures. They are often generated by calculating the long-term mean and range by averaging multiple sets of experimental duplicates over time. By doing such calculations, the laboratory can establish an expected average and variation for future comparison. Control charts thus provide a standard against which the stability of the lab performance can be evaluated.
Other QC procedures that ensure that the laboratory results are of required quality include instrument calibration, use of reference materials, repeated analyses and sample and reagent blank analyses.
Traceability, uncertainty and proficiency testing are the three major items to be addressed in a QA program. Traceability refers to assurance that the measurement results can be related to a reference through a documented, unbroken chain of comparisons. For example, the bias, precision and accuracy of testing can be determined by testing a certified reference material and comparing the laboratory results with the certified value. The certified value of the reference material is generally reported with uncertainty such that the comparison is of statistical significance. Proficiency tests serve as the external QA when the laboratory participates in a proficiency sample test program organized outside of the laboratory. Proficiency testing is an interlaboratory comparison, in which a number of labs conduct testing methods within their own lab on the same material and report the results to the organizing party. Each individual laboratory is then evaluated for performance based on statistical calculations. To establish required proficiency, the laboratory needs to maintain an appropriate schedule to participate in a proficiency test program.
ISO Standards and Accreditation
One critical part of the quality system is assessment, which means performance is measured against a standard. In 1947, the International Organization for Standardization (ISO) was created, and industry began to work on standards. In terms of laboratory quality systems, the relevant ISO standards are ISO 9000, which addresses quality management issues, and ISO 17025 and 15189, which address requirements for testing and calibration laboratories and medical laboratories, respectively. ISO 17025:2005 comprises five elements: scope, normative references, terms and definitions, management requirements and technical requirements, with the last two being the main sections. Management requirements cover specifications of the organization, management system, document control, review of requests, tenders and contracts, subcontracting of tests and calibration, purchasing services and supplies, complaints, improvements, corrective action, preventive action, control of records, internal audits and management reviews. Technical requirements deal with personnel issues, space and environmental conditions, test and calibration methods and method validation, equipment, measurement traceability, sampling, handling of test and calibration items, ensuring the quality of test and calibration results and reporting the results. For most testing and calibration laboratories, the ISO 17025 standard—“General requirements for the competence of testing and calibration laboratories”—is the benchmark for accreditation. This standard does not require that particular procedures be used in a laboratory but rather specifies the performance requirements for the procedures in a quality system. In other words, under the ISO 17025:2005 system, laboratories can determine their own pattern for carrying out procedures; however, an auditor or assessor may require justification for doing so. For example, the laboratory can use standard methods, nonstandard methods or methods developed in-house for testing, provided method validation has been performed and documented. The laboratory can also choose any methods and/or software for document control. The guiding principle behind ISO 17025 is the implementation of “fit for purpose” processes that can sustain continual quality improvement.
Accreditation involves a third party or an accreditation body attesting to the technical competence of a laboratory based on a set of accepted standards. Accreditation bodies cite ISO 17025:2005 as the gold standard for laboratory assessment. Even though different countries utilize different mechanisms to pursue accreditation, ISO is the global language for laboratories to exchange quality information. The International Laboratory Accreditation Cooperation is the collaboration of accreditation bodies working on development and harmonization of accreditation practices. In the U.S., there are a handful of accreditation bodies. Examples are the American Association for Laboratory Accreditation, Perry Johnson Laboratory Accreditation, Lab Accreditation Bureau and ANSI-ASQ National Accreditation Board. A typical accreditation process will take months to years, depending on the maturity of the existing laboratory quality practices. Finally, laboratory accreditation does not guarantee that the laboratory is of high quality, but it helps give customers confidence that the lab is capable of producing quality data.
Future Perspectives
Over the last 100 years, there has been a revolution in the implementation of quality systems for laboratories. In the pharmaceutical sector, numerous QA components have been incorporated, including Good Laboratory Practices and Good Clinical Practices. Concurrently, new tools for quality management systems have also emerged. These include software programs to implement QC activities and statistical analysis, new automation programs to facilitate laboratory efficiency, increased training and consultation programs to improve the qualification of personnel, etc. Implementation of the quality system requires resources and investment, so there is a significant cost to quality. ISO accreditation is not an inexpensive process either, as it requires personnel input, resources and capital investment.
The same quality standards and practices that have been established in the pharmaceutical industry are relevant to the food testing laboratory. One aspect of the 2011 Food Safety Modernization Act was its focus on “increasing the number of qualified laboratories that are eligible to perform testing” and on laboratory accreditation. In the future, laboratory accreditation in food testing will be the trend for both regulatory agencies and industry, given that accreditation is a good practice to gain consumer confidence and increasing international trade has expanded food safety into a global business. Such movements will continue to drive the market for high-quality lab testing. Eventually, the maturity of the laboratory quality system in the food industry will depend upon market, trade and regulatory needs.
Susie Y. Dai, Ph.D., is a research assistant professor in the Office of the Texas State Chemist and Department of Veterinary Pathobiology at Texas A&M University.
Looking for a reprint of this article?
From high-res PDFs to custom plaques, order your copy today!