View from the Specialty Tea Industry: Extending the Food Safety Net
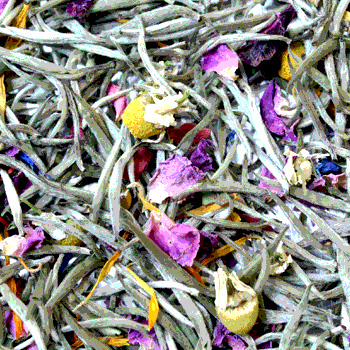
New rules to strengthen assurances that imported foods meet the same safety standards as food produced domestically will shift accountability to importers.
The Foreign Supplier Verification Program (FSVP) is a proposal under review by the U.S. Food and Drug Administration (FDA) that requires importers to verify that their foreign suppliers are implementing the modern, prevention-oriented food safety practices called for in the Food Safety Modernization Act (FSMA).
The draft regulations require importers to develop, maintain and follow a specific plan for each food type, to insure compliance with FSMA regulations as well as analyze and control potential hazards. If a breech occurs, importers must take corrective action.
In situations where the hazard could result in serious health consequences or death, the importer is required to do an onsite audit of the foreign supplier or demonstrate that an onsite audit has been conducted. Samples and testing and a review of food safety records would suffice in those instances where the hazard is not life threatening.
One of the first steps in addressing FSMA is for the importer to conduct a Hazard Analysis of each food product imported. Based on this analysis, there needs to be a fundamental determination of who will be responsible for managing that hazard physically—the supplier or the importer—and where that work will be conducted. Should that burden be addressed by the supplier, the challenge for the global supply chain will be to determine how suppliers can demonstrate control in an international arena.
A second proposed rule on the Accreditation of Third-Party Auditors/Certification Bodies would strengthen the quality, objectivity and transparency of foreign food safety audits on which many U.S. food companies and importers currently rely to help manage the safety of their global food supply chains.
U.S. food importers are always sensitive to costs and look to invest quality assurance resources in processes and technologies that offer the best value. Food companies continue to see an increasing number of audits per year and the need for documentation supplied to clients annually is rising exponentially. With FSMA and FSVP, this responsibility will work its way up the supply chain.
What we need to do with FMSA is to educate our suppliers on the changing regulatory environment in the United States. This is not an easy task, as some suppliers are reluctant to change, whereas others may find it easier to simply sell their products to other countries. On the other hand, those suppliers who can upgrade their systems and centralize on accepted food quality standards will benefit from accredited third party audits, just as QTrade Teas & Herbs has done in the United States. There is a global effort to standardize food safety practices through the Global Food Safety Initiative, but many of these markets are still pretty underdeveloped.
While agricultural products like processed tea and herbs pose few threats to public health, the variety and large number of ingredients that are added to tea require vigilance. The share of tropical products (coffee, cocoa, tea and spices) imported to the United States is nearly 100 percent since domestic production is close to zero. This means importers like QTrade Teas & Herbs deal almost exclusively with foreign suppliers. Many companies within our industry are traders who rely heavily on documentation and testing offered by the supplier. Food manufacturers such as ourselves are relatively more versed in both preparing for audits and conducting audits, looking for key program elements that pose significant health risks. Overall, I believe manufactures will be better prepared for FSMA than importers who function solely as brokers.
Pressures to elevate quality programs are not solely the result of changing governmental regulation, but also from retail brands wishing to the mitigate risk of product recalls. With each larger contract, companies invest more heavily in quality safeguards. Management needs to be sold on the responsibility for quality, as it’s all too easy to unwisely assign responsibility blindly to international suppliers.
Increasing Imports
Imports account for an increasing share of food consumed in the United States, estimated at 17 percent of the nation’s annual diet or 358 pounds per person, up from 11 percent in the early 1990s, according to the United States Department of Agriculture (USDA).
In 2000, the World Health Organization (WHO) established the Global Foodborne Infections Network to compile statistics and track incidents. WHO reports a rise in the number of people in developed countries becoming ill from foodborne diseases each year. Due to the globalization of food marketing and distribution food products, both accidentally and deliberately contaminated food can affect the health of people in numerous countries at the same time. “Foodborne diseases cannot only spread faster, they appear to be emerging more rapidly than ever before and are able to circumvent conventional control measures,” according to the WHO report establishing the Foodborne Disease Burden Epidemiology Reference Group.
One in six Americans becomes ill from foodborne diseases annually with 128,000 cases that are serious enough to require hospitalization and more than 3,000 deaths, according to the Centers for Disease Control and Prevention (CDC). The CDC estimates that if we could prevent 10 percent of foodborne illness, there would be five million fewer Americans who get sick each year. The majority of incidents are domestic since only 7 percent of the food Americans consume is from overseas but each year there are incidents involve imported foods despite the fact that FDA rejects millions of pounds of food at the nation’s borders.
“The annual cost of the illnesses associated with imported foods that would be subject to the FSVP regulations is approximately $1.18 billion, which is more than one-fifth of the entire estimated burden of illness related to foods consumed in the United States,” according to FDA.
The challenge ahead is convincing a global supply chain to embrace and manage FSMA regulations while meeting the new requirements of the Sanitary Food Transportation Act.
Reputable suppliers recognize that food safety is a priority. Government oversight for domestic consumption is vigilant and third-party auditors and regulators visit farms and processing facilities. Bridges of trade linking most of the world’s tea suppliers to America are anchored with strong abutments. Trade in herbs and spices with Europe and tea with most of the industrialized nations are secure, but that is not the case with developing countries where small holders produce the majority of foods.
Global Concern
Thirty years after several lethal incidents, the European Union’s import/export regulations are some of the toughest. Imports from Mexico, Brazil and Australia are similarly regulated. QTrade’s most important trading partner is currently implementing the Safe Food for Canadians Act.
China is making progress. The country put its first Food Safety Law into effect in June 2009, following a tainted-milk scandal that sickened 300,000 babies, hospitalized 54,000 and killed 11 children under 3 years of age. Toxic melamine added to milk involved 21 producers. Testing of dairy products is much more extensive today but food safety issues still abound. In October 2013, China’s Food and Drug Administration released a revised draft of the new Food Safety Law on its website, asking for public comments through November.
The 22,000-word draft draws half its content from the previous law. Revisions are primarily to clarify responsibility. The China Food and Drug Administration is designated as the main overseer with the Ministry of Health assigned to set standards and assess risk; the Administration of Quality Supervision Inspection and Quarantine is in charge of food imports and exports and the Ministry of Public Security charged with policing companies and individuals that break the law.
This is important as China is the world’s largest agricultural exporter with products valued at $848 billion in 2010. It is also one of the most decentralized food suppliers with 200 million farming households with average land holdings of one to two acres per farm and at least 400,000 food processing enterprises, most with 10 or fewer employees.
Chinese food exports comprise 14 percent of the world market, up from 8 percent in 2001. China first appeared among the nation’s top 15 agricultural import sources in 1993 and has since advanced to become the fourth largest supplier of horticultural products to the United States.
Pew Research’s Global Attitudes Project found that 41 percent of urban Chinese believed food safety to be a “very big problem,” more than three times higher compared with 2008 and now at similar levels to other widespread concerns such as corruption and inequality, according to the U.S.-China Health Products Association.
“In the West, food safety concerns are largely about tracing problems in complicated systems of mass food production. In China, however, concerns are very much a fear of being cheated by unscrupulous business people chasing profits by selling inferior or even toxic goods,” according to the U.S.-China Health Products Association.
“The Chinese government is also highly engaged in solving the problem. Xi Jinping, China’s new president, openly alluded to fixing China’s food-safety record even before he came into office. At the recent National People’s Congress in March, the State Food and Drug Administration, formerly regulated by the Ministry of Health, was elevated to full ministerial status. This was part of a range of legal and administrative initiatives to address the fragmentation inherent in China’s food safety regulatory framework,” according to the U.S.-China Health Products Association.
China grows 35 percent of the world’s tea and is the largest supplier of green tea. The Food and Agriculture Organization of the United Nations projections to 2017 indicate that world green tea production is expected to grow at a considerably faster rate than black tea, 4.5 percent annually compared to 1.9 percent for black tea.
Tea imports from China have been steadily rising since 2001. The wholesale price of direct imports totaled $126 million in 2012, about 20 percent of the nation’s supply according to USDA. An additional $105 million worth of tea, much of it green, was imported from Canada. China is the largest supplier of green tea to Canada.
Reasonably Likely to Occur
QTrade’s supply chain is anchored on five continents, with the important task of ensuring the safety of imported ingredients. Oversight extends through the blending, manufacturing and packaging of both conventional and USDA National Organic Program-certified teas for customers that buy as little as five kilos to several full containers per month.
Tea is not a high-risk food. People traditionally consume the liquor not the leaf, but the combination of tea with fruits, nuts, spices and herbs requires the same diligence as any food processor.
FDA is proposing a flexible, risk-based approach to foreign supplier verification. The proposed regulation focuses on foreseeable food safety risks identified through a hazard assessment process, rather than all risks covered by the adulteration provisions in the Food Drug and Cosmetics Act.
In the tea industry, the greatest source of risk is in the form of microbiological and chemical contamination, as well as the proper handling of allergens. The former is addressed by testing products with a certified domestic laboratory, while the latter is addressed by proper labeling and segregation of ingredients and equipment used to handle allergens. One of the most important lessons we’ve learned these past two years is we can build systems to handle these risks effectively, but they will be more effectively handled through the adoption of new technologies. We have incorporated many verifications steps in production—these are all better handled via electronic signatures and cleaner presentation of data entry and reporting systems.
Third-Party Auditors
Certified auditors operating on foreign soil are central to a global system that provides significantly elevated assurances about the safety of FDA-regulated food moving in international trade in a more efficient way.
One of the FSMA mandates directs FDA to establish a program for the Accreditation of Third-Party Auditors for foreign food facilities. Under this program, FDA would recognize accreditation bodies, which would in turn accredit third-party auditors to, among other things, conduct food safety audits and issue certifications for foreign facilities and food under specified programs.
The proposed rule, as described by FDA, contains requirements relating to auditing and certification of foreign food facilities and food under the program and for notifying FDA of conditions in an audited facility that could cause or contribute to a serious risk to the public health.
“The proposed requirements for monitoring, oversight, and notification are needed to give the FDA, consumers and other stakeholders confidence in the program,” according to FDA. Third-party auditors can be foreign governments, foreign cooperative or other third party.
The central premise is that auditors “meet standards for legal authority, competency and capacity, impartiality/objectivity, quality assurance and records procedures.”
Although the FSVP’s proposal does not require the use of accredited third-party auditors, FDA anticipates that once the FDA accreditation system is in place, importers may increasingly rely on audits by accredited third parties to meet their supplier verification requirements under FSVP.
In preparation for third party audits, consider alternatives to pre-assess the capabilities of your suppliers. This can be done simply by asking your suppliers to complete a detailed questionnaire of their policies and certifications. Certainly if you have an opportunity to conduct this pre-assessment yourself when visiting the site, you will be able to offer guidance prior to an FDA accreditation audit.
A couple of years ago, our choice was whether to invest and try to stay ahead of the curve, or to wait until government more fully regulates how we manage quality. By acting quickly to invest heavily in upgrading the talents of our quality assurance staff, procedures and policies, the entire organization can be proud of the numerous changes we have adopted. Of course, what remains is the need to apply what we have learned to our international network of suppliers.
Ronald Eng is vice president of quality assurance at QTrade Teas and Herbs. To learn more, please visit www.QTradeTeas.com.
>
Looking for a reprint of this article?
From high-res PDFs to custom plaques, order your copy today!